Dynamic crack tip stress field measuring method and device
A crack tip and stress field technology, applied in the field of stress field experimental research, can solve problems such as the influence of manual proficiency, the accuracy of measurement results, and complex operations
- Summary
- Abstract
- Description
- Claims
- Application Information
AI Technical Summary
Problems solved by technology
Method used
Image
Examples
Embodiment 1
[0054] see figure 1 As shown, the embodiment of the present invention is a dynamic crack tip stress field measurement method, which can be applied to the measurement of various stress fields including the dynamic crack tip, including steps: S1, using digital image acquisition equipment to obtain the test piece surface affected Loading images before and after deformation; S2, searching in the post-deformation image for a sub-area where the second mass point is located that matches the sub-area where the first mass point is located in the image before deformation; S3, calculating the displacement information of the first mass point before and after deformation; S4. Calculate the stress field according to the displacement information of the first mass point.
[0055] An embodiment of the present invention is a method for measuring the stress field at the tip of a dynamic crack. By searching the deformed image for the sub-area where the second mass point is located that matches th...
Embodiment 2
[0062] see figure 2 As shown, the embodiment of the present invention provides a dynamic crack tip stress field measurement system, including: an image acquisition device 1 and a digital image processing device 2; Converting the image into a digital signal and sending it to the digital image processing device; the digital image processing device is used to search for a sub-region where the first particle is located in the image after deformation that matches the sub-region where the first particle is located in the image before deformation. area; calculating the displacement information of the first mass point before and after deformation; calculating the stress field through the displacement information of the first mass point.
[0063] In the measurement system described in this embodiment, since the image processing device searches the deformed image for the sub-area where the second mass point is located that matches the subsystem where the first displaced mass point is l...
PUM
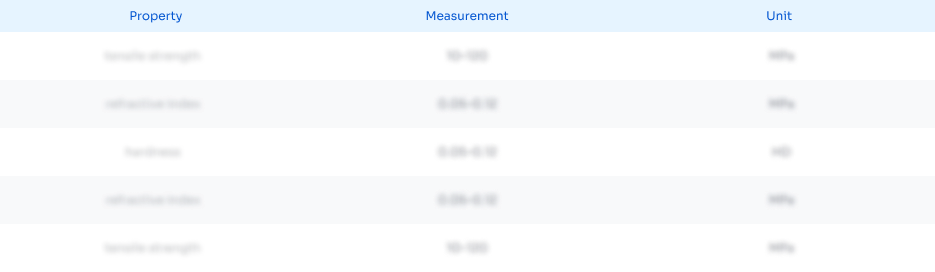
Abstract
Description
Claims
Application Information

- Generate Ideas
- Intellectual Property
- Life Sciences
- Materials
- Tech Scout
- Unparalleled Data Quality
- Higher Quality Content
- 60% Fewer Hallucinations
Browse by: Latest US Patents, China's latest patents, Technical Efficacy Thesaurus, Application Domain, Technology Topic, Popular Technical Reports.
© 2025 PatSnap. All rights reserved.Legal|Privacy policy|Modern Slavery Act Transparency Statement|Sitemap|About US| Contact US: help@patsnap.com