A kind of tar residue resource treatment process
A treatment process and a technology for tar residue, which are applied in the field of tar residue resource treatment technology, can solve the problems of less obvious separation effect and complicated process flow, and achieve the effects of simplifying separation links, low energy consumption and energy saving.
- Summary
- Abstract
- Description
- Claims
- Application Information
AI Technical Summary
Problems solved by technology
Method used
Image
Examples
Embodiment 1
[0033] The tar residue recycling process of the present embodiment comprises the following steps:
[0034] (1) Inject the alkylphenol formaldehyde resin and cationic polyacrylamide into the process of conveying the raw material tar residue and mix them evenly. The volume ratio of the alkylphenol formaldehyde resin to the cationic polyacrylamide is 2:1. The mixing amount of acrylamide is 200mg of tar residue per liter, that is, the dosage is 200mg / L. Once the material enters the static tank, it is stirred at a constant temperature of 40°C and a stirring speed of 120r / min for 2h, and then stands at 25°C for 4h. About 47wt% of moisture, the sedimentation material at the bottom of the tower (accounting for 53wt% of the raw material) is sent to the process raw material storage tank for standby.
[0035] (2) The tar residue dehydrated and demulsified in step (1) and the composite extractant are mixed and preheated to 45°C in the pipeline in front of the tower according to the mass r...
Embodiment 2
[0043] The tar residue recycling process of the present embodiment comprises the following steps:
[0044] (1) Inject ethylene oxide and cationic polyacrylamide during the transportation of raw material tar residue and mix them uniformly. The volume ratio of ethylene oxide and cationic polyacrylamide is 1.5:1. The mixing amount of acrylamide is 200 mg of tar residue per liter, that is, the dosage is 200 mg / L. Material 2 enters the static tank and stirs for 2 hours at a constant temperature of 35 °C with a stirring speed of 100 r / min, and stands at 20 °C for 3 hours. About 45wt% of moisture, the sedimentation material at the bottom of the tower (accounting for 55wt% of the raw material) is sent to the process raw material storage tank for standby.
[0045] (2) The tar residue dehydrated and demulsified in step (1) and the composite extractant are mixed and preheated to 50°C in the pipeline in front of the tower according to the mass ratio of 1.5:1 and then sent to the thermal e...
Embodiment 3
[0052] The tar residue recycling process of the present embodiment comprises the following steps:
[0053] (1) Polyethylene polyammonia and cationic polyacrylamide are injected into the raw material tar residue transportation process and mixed evenly. The volume ratio of polyethylene polyammonia and cationic polyacrylamide is 1:1. The mixing amount of acrylamide is 100 mg of tar residue per liter, that is, the dosage is 100 mg / L. Once the material enters the static tank, it is stirred at a constant temperature of 50 °C and a stirring speed of 60 r / min for 1 h, and is left at 20 °C for 4 h. The bottom settled material is sent to the process raw material storage tank for standby.
[0054] (2) The tar residue dehydrated and demulsified in step (1) and the composite extractant are mixed and preheated to 50°C in the pipeline in front of the tower according to the mass ratio of 2:1, and then sent to the thermal extraction tower. The extraction condition is temperature 50℃, pressure...
PUM
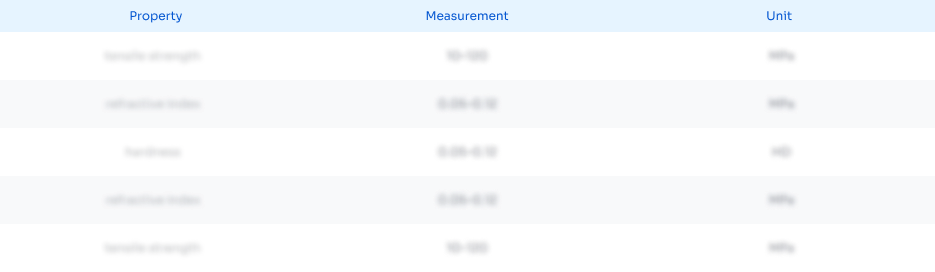
Abstract
Description
Claims
Application Information

- R&D
- Intellectual Property
- Life Sciences
- Materials
- Tech Scout
- Unparalleled Data Quality
- Higher Quality Content
- 60% Fewer Hallucinations
Browse by: Latest US Patents, China's latest patents, Technical Efficacy Thesaurus, Application Domain, Technology Topic, Popular Technical Reports.
© 2025 PatSnap. All rights reserved.Legal|Privacy policy|Modern Slavery Act Transparency Statement|Sitemap|About US| Contact US: help@patsnap.com