Positioning device for steel plate numerical control cutting and positioning method
A positioning device and steel plate technology, applied in auxiliary devices, welding/cutting auxiliary equipment, welding/welding/cutting items, etc., can solve the problems of small cutting allowance, poor positioning accuracy, non-coil delivery, etc., and achieve simple operation , The effect of high positioning accuracy
- Summary
- Abstract
- Description
- Claims
- Application Information
AI Technical Summary
Problems solved by technology
Method used
Image
Examples
Embodiment Construction
[0056] Such as Figure 1 to Figure 5 and Figure 7 The shown positioning device for numerically controlled cutting of steel plates includes a first positioning mechanism and a second positioning mechanism that are installed on the operating platform 16 of the cutting machine and position the steel plate 18 to be cut. The second positioning mechanism is located on the same side of the steel plate 18 to be cut;
[0057] The first positioning mechanism includes a first base plate 1, a first sliding seat installed on the first base plate 1 and capable of sliding along the length direction of the first base plate 1, and a first sliding seat installed on the first base plate and to be cut. The first positioning plate 2 for positioning the steel plate 18;
[0058] The second positioning mechanism includes a second base plate 3, a second sliding seat that is installed on the second base plate 3 and can slide along the length direction of the second base plate 3, and is installed on ...
PUM
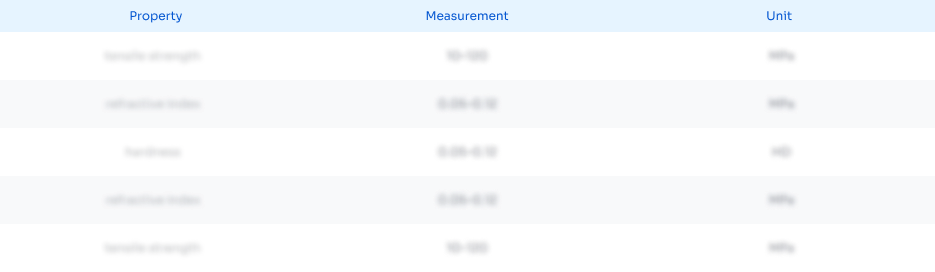
Abstract
Description
Claims
Application Information

- R&D Engineer
- R&D Manager
- IP Professional
- Industry Leading Data Capabilities
- Powerful AI technology
- Patent DNA Extraction
Browse by: Latest US Patents, China's latest patents, Technical Efficacy Thesaurus, Application Domain, Technology Topic, Popular Technical Reports.
© 2024 PatSnap. All rights reserved.Legal|Privacy policy|Modern Slavery Act Transparency Statement|Sitemap|About US| Contact US: help@patsnap.com