Efficient CAE simulation optimal analysis method for aluminium alloy mortise-and-tenon joint structure
A connection structure and analysis method technology, applied in special data processing applications, instruments, electrical digital data processing, etc., can solve problems such as large CAE model files, rigidity of mortise joint structure, poor model iteration utilization, etc., to achieve simplified construction Modeling, short calculation time, and realistic simulation results
- Summary
- Abstract
- Description
- Claims
- Application Information
AI Technical Summary
Problems solved by technology
Method used
Image
Examples
specific Embodiment
[0018] Such as Figure 1~3 As shown, the example prototype of beam 1 in the analysis object of the present invention is a 45*31 aluminum alloy profile, and the example prototype of longitudinal beam 2 is a 45*65 aluminum alloy profile. Beam 1 represents beam 5, beam unit represents longitudinal beam 2, represents longitudinal beam 6, and spring unit 7; represents beam 5, which shows the cross section of the beam unit, and then beam 8, which shows the cross-sectional shape of the beam unit, and represents longitudinal beam 6 After the section of the beam unit is the longitudinal beam 9 showing the cross-sectional shape of the beam unit, the beam 8 showing the cross-sectional shape of the beam unit and the longitudinal beam 9 showing the cross-sectional shape of the beam unit represent the cross-section state attributes of the beam 5 and the longitudinal beam 6 respectively. Beam 5, that is, the beam 8 showing the cross-sectional shape of the beam unit is used to simulate the be...
PUM
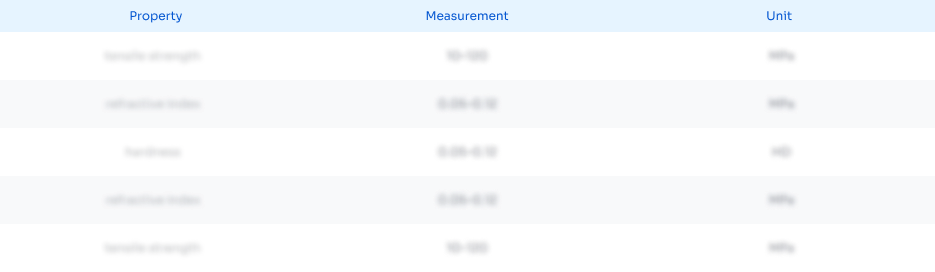
Abstract
Description
Claims
Application Information

- R&D
- Intellectual Property
- Life Sciences
- Materials
- Tech Scout
- Unparalleled Data Quality
- Higher Quality Content
- 60% Fewer Hallucinations
Browse by: Latest US Patents, China's latest patents, Technical Efficacy Thesaurus, Application Domain, Technology Topic, Popular Technical Reports.
© 2025 PatSnap. All rights reserved.Legal|Privacy policy|Modern Slavery Act Transparency Statement|Sitemap|About US| Contact US: help@patsnap.com