Cutter shaft vector optimization method based on covariant field functionals
A tool axis vector and optimization method technology, applied in the field of milling, can solve problems such as overcutting between the tool and the workpiece or collision with the smoothness of the tool axis vector trajectory, and achieve the effects of reducing the difficulty of solving, high use value, and wide application range
- Summary
- Abstract
- Description
- Claims
- Application Information
AI Technical Summary
Problems solved by technology
Method used
Image
Examples
Embodiment Construction
[0063] In order to make the object, technical solution and advantages of the present invention clearer, the present invention will be further described in detail below in conjunction with the accompanying drawings and embodiments. It should be understood that the specific embodiments described here are only used to explain the present invention, not to limit the present invention. In addition, the technical features involved in the various embodiments of the present invention described below can be combined with each other as long as they do not constitute a conflict with each other.
[0064] figure 2 It is a schematic diagram of the structure of the tool axis vector in the actual machining of the numerical control machining constructed according to the preferred embodiment of the present invention, such as figure 2 As shown, the tool contact, referred to as CC point, refers to the position point tangent to the workpiece surface and the tool surface during the process of mi...
PUM
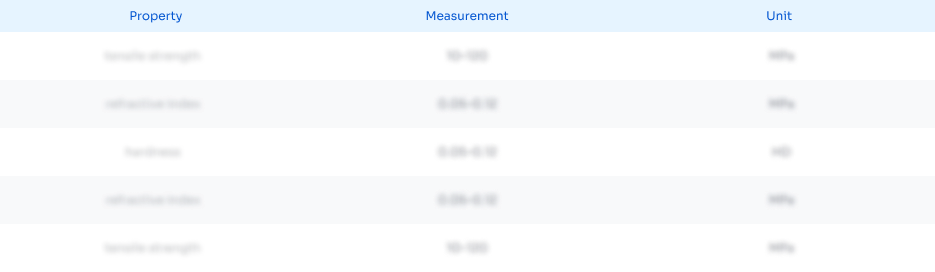
Abstract
Description
Claims
Application Information

- R&D
- Intellectual Property
- Life Sciences
- Materials
- Tech Scout
- Unparalleled Data Quality
- Higher Quality Content
- 60% Fewer Hallucinations
Browse by: Latest US Patents, China's latest patents, Technical Efficacy Thesaurus, Application Domain, Technology Topic, Popular Technical Reports.
© 2025 PatSnap. All rights reserved.Legal|Privacy policy|Modern Slavery Act Transparency Statement|Sitemap|About US| Contact US: help@patsnap.com