Calibration device for six-degree-of-freedom force and torque sensor
A technology of torque sensor and calibration device, which is applied in the direction of measuring device, force/torque/power measuring instrument calibration/testing, instruments, etc. Easy and fast replacement
- Summary
- Abstract
- Description
- Claims
- Application Information
AI Technical Summary
Problems solved by technology
Method used
Image
Examples
Embodiment Construction
[0024] The principles and features of the present invention are described below in conjunction with the accompanying drawings, and the examples given are only used to explain the present invention, and are not intended to limit the scope of the present invention.
[0025] like Figure 1-Figure 5 As shown, a calibration device of a six-degree-of-freedom force and moment sensor, including a lifting mechanism 1, a six-degree-of-freedom motion tooling 2 of a stewart structure, and a six-degree-of-freedom force and moment measurement tooling 3 of a stewart structure, the six-degree-of-freedom motion The tooling 2 is installed upside down on the bottom of the lifting mechanism 1, and can move up and down with the lifting mechanism 1. The six-degree-of-freedom force and moment measuring tooling 3 is located below the six-degree-of-freedom motion tooling 2. The measured six-degree-of-freedom force and moment sensor 5 is fixed between the six-degree-of-freedom motion tooling 2 and the ...
PUM
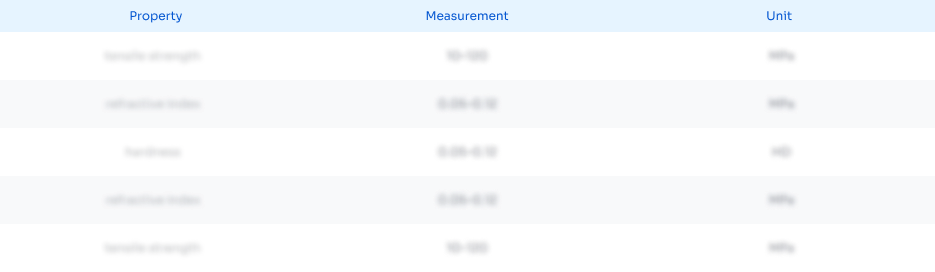
Abstract
Description
Claims
Application Information

- R&D Engineer
- R&D Manager
- IP Professional
- Industry Leading Data Capabilities
- Powerful AI technology
- Patent DNA Extraction
Browse by: Latest US Patents, China's latest patents, Technical Efficacy Thesaurus, Application Domain, Technology Topic, Popular Technical Reports.
© 2024 PatSnap. All rights reserved.Legal|Privacy policy|Modern Slavery Act Transparency Statement|Sitemap|About US| Contact US: help@patsnap.com