Metal casting system and method
A metal and molten metal technology, applied in the field of metal melting and casting systems, can solve problems such as temperature reduction, equipment cost increase, and safety accidents.
- Summary
- Abstract
- Description
- Claims
- Application Information
AI Technical Summary
Problems solved by technology
Method used
Image
Examples
Embodiment Construction
[0027] figure 1 A metal die casting system 100 according to an embodiment of the present invention is shown. The metal casting system 100 may include: a melting furnace 101 for melting metal, the melting furnace 101 includes a melting furnace outlet 1013; one or more die casting devices 103 for forming metal blanks; a pretreatment device for melting the molten metal Transfer to die casting device 103. figure 1 Two embodiments of die casting devices are shown in. Such as figure 2 As shown, the pretreatment device communicates with the melting furnace 101 so that the molten metal in the melting furnace 101 can pass through the melting furnace outlet 1013. figure 2 The arrow in the middle (in the pretreatment device) flows into the pretreatment device, and the pretreatment device communicates with the die casting device 103 so that the molten metal can be delivered to the die casting device 103 for die casting.
[0028] According to the embodiment of the present invention, the met...
PUM
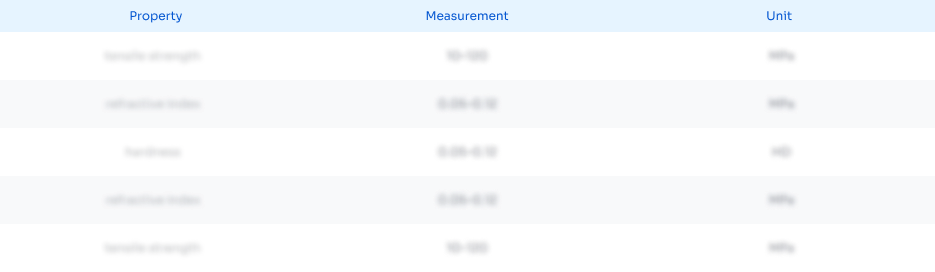
Abstract
Description
Claims
Application Information

- R&D Engineer
- R&D Manager
- IP Professional
- Industry Leading Data Capabilities
- Powerful AI technology
- Patent DNA Extraction
Browse by: Latest US Patents, China's latest patents, Technical Efficacy Thesaurus, Application Domain, Technology Topic, Popular Technical Reports.
© 2024 PatSnap. All rights reserved.Legal|Privacy policy|Modern Slavery Act Transparency Statement|Sitemap|About US| Contact US: help@patsnap.com