Liquid crystal display panel and manufacturing method for same
A technology for liquid crystal display panels and manufacturing methods, applied in nonlinear optics, instruments, optics, etc., can solve the problems of increased space cost, low controllability, complex design and manufacturing process, etc., to reduce the blocking effect and increase the tilt angle θ , the effect of saving arrangement space
- Summary
- Abstract
- Description
- Claims
- Application Information
AI Technical Summary
Problems solved by technology
Method used
Image
Examples
Embodiment Construction
[0041] In order to further illustrate the technical means adopted by the present invention and its effects, the following describes in detail in conjunction with preferred embodiments of the present invention and accompanying drawings.
[0042] see figure 1 , the invention provides a method for manufacturing a liquid crystal display panel, comprising the steps of:
[0043] Step 1, such as figure 2 and image 3 As shown, a first substrate 10 and a second substrate 20 are provided, a first photoresist film 31 is formed on the first substrate 10, and a second photoresist film 32 is formed on the first photoresist film 31; The photosensitive characteristics of the first photoresist film 31 and the second photoresist film 32 are different, that is, the first photoresist film 31 and the second photoresist film 32 have different light reaction absorption wavelengths, or the first photoresist film 31 and the second photoresist film 32 have different photoresponse sensitivities to ...
PUM
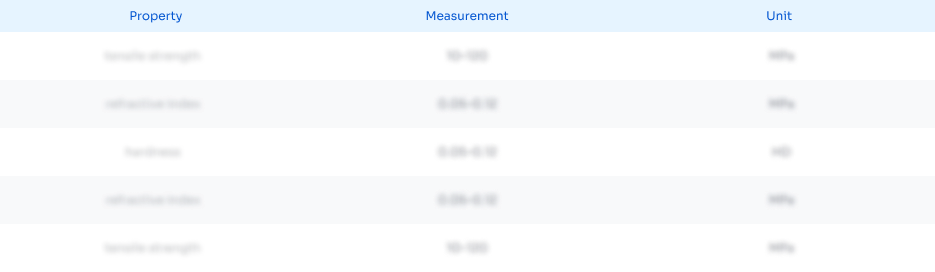
Abstract
Description
Claims
Application Information

- R&D Engineer
- R&D Manager
- IP Professional
- Industry Leading Data Capabilities
- Powerful AI technology
- Patent DNA Extraction
Browse by: Latest US Patents, China's latest patents, Technical Efficacy Thesaurus, Application Domain, Technology Topic, Popular Technical Reports.
© 2024 PatSnap. All rights reserved.Legal|Privacy policy|Modern Slavery Act Transparency Statement|Sitemap|About US| Contact US: help@patsnap.com