Retreat-stopping mechanism for preventing injection-moulded part from sticking to mould during core-pulling retreat
A technology of injection molded parts and sticky molds, which is applied in the field of mold core-pulling design, can solve problems such as difficulty in meeting the injection precision requirements of slender parts, deformation of injection molded parts, product deformation, etc., and achieves easy implementation and promotion, stable performance, and simple structure Effect
- Summary
- Abstract
- Description
- Claims
- Application Information
AI Technical Summary
Problems solved by technology
Method used
Image
Examples
Embodiment Construction
[0022] The invention discloses an anti-retraction mechanism (referred to as the anti-retraction mechanism) for preventing injection molded parts from sticking to the mold when the core is pulled back. Molds for long plastic parts. Guide the injection molded part 1 with a kind of elongated car light below (that is, a kind of injection molding product, such as figure 1 Shown) as an example to illustrate the structure and working principle of the anti-retraction mechanism. The position of the end 11 of the headlight guide injection molded part of the car has a situation of demoulding and undercutting, so a core-pulling structure needs to be provided. However, due to the slender shape of the injection molded part, simple core pulling can easily cause serious deformation of the product, resulting in distortion of the optical reflection surface and affecting the product effect. The anti-retraction mechanism of the present invention is added to the core-pulling structure, and is es...
PUM
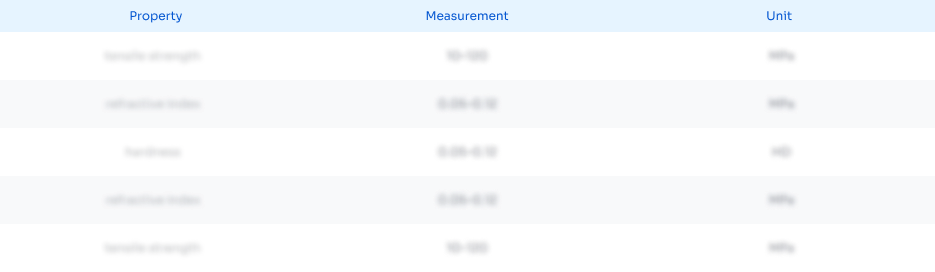
Abstract
Description
Claims
Application Information

- R&D
- Intellectual Property
- Life Sciences
- Materials
- Tech Scout
- Unparalleled Data Quality
- Higher Quality Content
- 60% Fewer Hallucinations
Browse by: Latest US Patents, China's latest patents, Technical Efficacy Thesaurus, Application Domain, Technology Topic, Popular Technical Reports.
© 2025 PatSnap. All rights reserved.Legal|Privacy policy|Modern Slavery Act Transparency Statement|Sitemap|About US| Contact US: help@patsnap.com