Flexible mechanical gripper and carrying robot with same
A mechanical and gripper technology, applied in the field of handling robots, can solve the problems of easily damaged packaging bags, large operating space, and damaged packaging bags, and achieve the effects of simple operation, flexible movement, and reduced labor intensity
- Summary
- Abstract
- Description
- Claims
- Application Information
AI Technical Summary
Problems solved by technology
Method used
Image
Examples
Embodiment Construction
[0048] The specific implementation manners of the present invention will be further described in detail below in conjunction with the accompanying drawings and embodiments.
[0049] Such as figure 1 As shown, the flexible mechanical gripper of the present invention is used for grabbing stacked bagged materials, which includes: a connecting frame 1, a flat plate 3, a double-acting cylinder, a driving mechanism, a transmission mechanism and a clamping mechanism.
[0050] The connecting frame 1 is a rectangular frame structure, and the top of the connecting frame 1 is detachably connected with the mechanical arm of the handling robot.
[0051] The plate 3 is affixed to the bottom of the connecting frame 1 through the plate connecting bolt group 7, and the plate 3 is a rectangular plate.
[0052] The double-acting cylinder includes a cylinder barrel 4 and a cylinder piston rod 5 . The cylinder barrel 4 of the double-acting cylinder is vertically arranged in the accommodation spa...
PUM
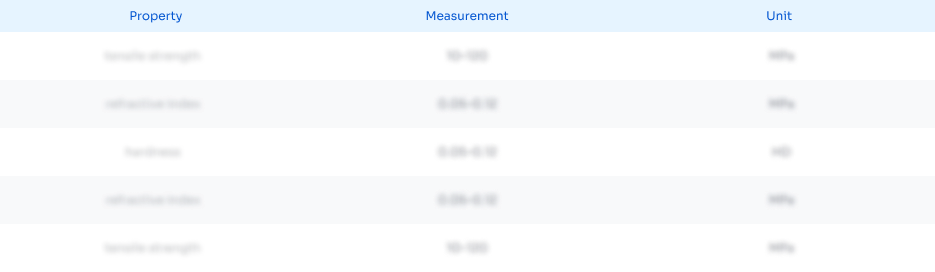
Abstract
Description
Claims
Application Information

- R&D
- Intellectual Property
- Life Sciences
- Materials
- Tech Scout
- Unparalleled Data Quality
- Higher Quality Content
- 60% Fewer Hallucinations
Browse by: Latest US Patents, China's latest patents, Technical Efficacy Thesaurus, Application Domain, Technology Topic, Popular Technical Reports.
© 2025 PatSnap. All rights reserved.Legal|Privacy policy|Modern Slavery Act Transparency Statement|Sitemap|About US| Contact US: help@patsnap.com