Short-tail vertical-lifting gyroplane
A technology of helicopter rotor and tail, applied in the field of rotorcraft, can solve the problems of maneuverability without helicopter rotorcraft, failure of autorotation rotorcraft to maximize safety, increased volume and unsafety, etc.
- Summary
- Abstract
- Description
- Claims
- Application Information
AI Technical Summary
Problems solved by technology
Method used
Image
Examples
Embodiment 1
[0007] refer to figure 1 , shown in 2,3,5,6,7, a kind of short tail helicopter rotorcraft comprises cockpit (21), single-layer main rotor (17), variable pitch propeller hub (16), second vertical axis ( 18), automatic swash plate (19), main gearbox (23), engine (24), tail propeller assembly (1), sliding wheel (27), frame (28), engine (24) passes through the main gearbox (23), connected with the second vertical shaft (18) and the tail propeller (1) assembly. The tail propeller structural assembly is divided into upper and lower parts, the upper part can be rotated Image 6 and fix the base below. The upper rotatable part has a first horizontal shaft (2) that can be used to install the blade of the autogyro tail propeller (1); The center stretches out, and a cross (30) perpendicular to the axis is installed on the same plane at the end of the stretch. There are connecting rods (36) on the edges of the four ends of the cross. The force arm (31) is connected, and one end of the...
Embodiment 2
[0009] refer to Figure 4 As shown, the overall structure is the same as that in Implementation 1, except that a separate speed-regulating motor (29) is used to provide power to the tail propeller (1), and an electric motor (29) and the tail propeller (1) are fixed on the same rotating base (37), the bottom of the base has a third vertical shaft (38), which is inserted into the round hole of the body and can rotate in the round hole. A connecting rod is installed on one side of the upper rotating shell, and the tail propeller can be controlled by pulling the connecting rod direction of blowing.
[0010] The present invention is characterized in that the tail propeller can change the blowing direction, and compared with the existing technology of the helicopter rotorcraft, the long tail can be shortened, the safety is increased, and the cruising speed is increased. Compared with autogyro aircraft, it can take off and land vertically, translate, hover, and fly in any direction ...
PUM
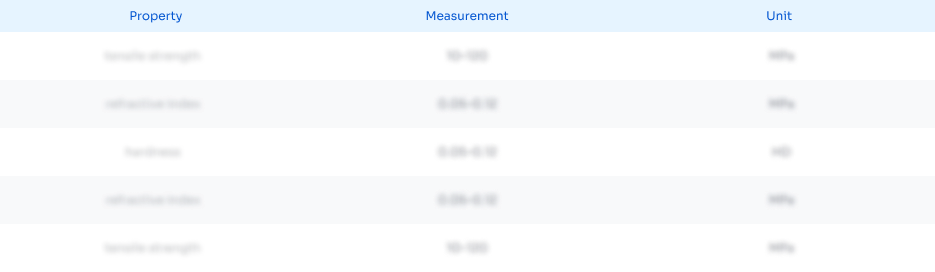
Abstract
Description
Claims
Application Information

- R&D
- Intellectual Property
- Life Sciences
- Materials
- Tech Scout
- Unparalleled Data Quality
- Higher Quality Content
- 60% Fewer Hallucinations
Browse by: Latest US Patents, China's latest patents, Technical Efficacy Thesaurus, Application Domain, Technology Topic, Popular Technical Reports.
© 2025 PatSnap. All rights reserved.Legal|Privacy policy|Modern Slavery Act Transparency Statement|Sitemap|About US| Contact US: help@patsnap.com