Positioning clamping device for machining of complex inner shape of thin-wall cylindrical workpiece
A thin-walled cylinder, positioning and clamping technology, used in positioning devices, metal processing equipment, metal processing machinery parts, etc. Convenience, ensure the shape and position tolerance, improve the effect of rigidity
- Summary
- Abstract
- Description
- Claims
- Application Information
AI Technical Summary
Problems solved by technology
Method used
Image
Examples
Embodiment Construction
[0032] The present invention will be further described below in conjunction with the accompanying drawings.
[0033] Such as Figures 1 to 6 As shown, the present invention includes a base 11 and a clip spring 2. The base 11 includes a base plate and a support 6 fixedly mounted on the base plate by screws 10. A calibration reference step 20 is provided on the side of the base plate as a calibration reference. The support 6 is cylindrical, and the top of the support 6 is provided with a taper sleeve 3 , and the upper part of the inner hole of the taper sleeve 3 is a second tapered surface 16 . The top of the support 6 is provided with a vertical guide groove 26, and the taper sleeve 3 is provided with a screw 12 corresponding to the guide groove, and the end of the screw 12 is placed in the guide groove, which can prevent the taper sleeve 3 from rotating and compressing the threaded sleeve 4. turn. The outer wall of the taper sleeve 3 is provided with an annular groove 24, an...
PUM
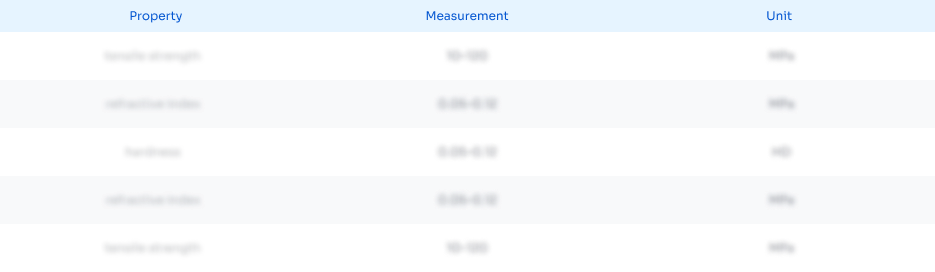
Abstract
Description
Claims
Application Information

- Generate Ideas
- Intellectual Property
- Life Sciences
- Materials
- Tech Scout
- Unparalleled Data Quality
- Higher Quality Content
- 60% Fewer Hallucinations
Browse by: Latest US Patents, China's latest patents, Technical Efficacy Thesaurus, Application Domain, Technology Topic, Popular Technical Reports.
© 2025 PatSnap. All rights reserved.Legal|Privacy policy|Modern Slavery Act Transparency Statement|Sitemap|About US| Contact US: help@patsnap.com