Suture having a restraining element at an end and method and use thereof
A suture and coil technology, applied in the field of self-retaining suture devices, can solve problems such as low-efficiency processing, ineffectiveness, loss of matrix fiber strength, etc.
- Summary
- Abstract
- Description
- Claims
- Application Information
AI Technical Summary
Problems solved by technology
Method used
Image
Examples
Embodiment 1
[0111] The welding die was constructed as a 0.133" diameter horn tip. The inner surface of the horn tip was fabricated with a flat rim surface of 0.010" width and a spherical concave surface of 0.125" diameter. The horn design Set on a 20kHz Branson welder. The unit was set to a fixed stop at 0.018". The weld pressure was set at 20 psi and the trigger pressure was set at 20 lbf. A 0.6 ratio step-down was used with the ultrasonic horn and the amplitude was set at 75%. The welder was set to weld at the energy imparted during the cycle and set to stop at an energy of 2.0J. The machine descending speed is set to 60.
[0112] Polydioxanone (PDS) 2 / 0 cylindrical fibers were utilized. Approximately 3.25" of fiber was wound into the jig and the welding cycle was initiated. The strength of the terminal attachment was measured using an Instron unit with a grooved metal clamp holding the terminated end of the fiber. The fiber was pulled until the terminal disengaged from the fiber . ...
Embodiment 2
[0116] The ultrasonic horn was set on a 20kHz Branson welder. The unit was set with a fixed stop at 0.018". Weld pressure was set at 25 psi and trigger pressure was set at 20 lbf. A 0.6 ratio pressure reducer was used with the ultrasonic horn and the amplitude setting At 70%. The welder was set to weld at the energy imparted during the cycle and set to stop at an energy of 2.1 J. The machine descent speed was set to 50.
[0117] Polydioxanone (PDS) 2 / 0 cylindrical fibers were utilized. Approximately 3.25" of fiber was wound into the jig and the welding cycle was initiated. The strength of the terminal attachment was measured using an Instron unit with a grooved metal clamp holding the terminated end of the fiber. The fiber was pulled until the terminal disengaged from the fiber .
[0118] Test results can be found at Figure 28 And it is reflected in Table 1 below:
[0119]
[0120] In both Example 1 and Example 2, the average terminal strength exceeded the USP knot ten...
PUM
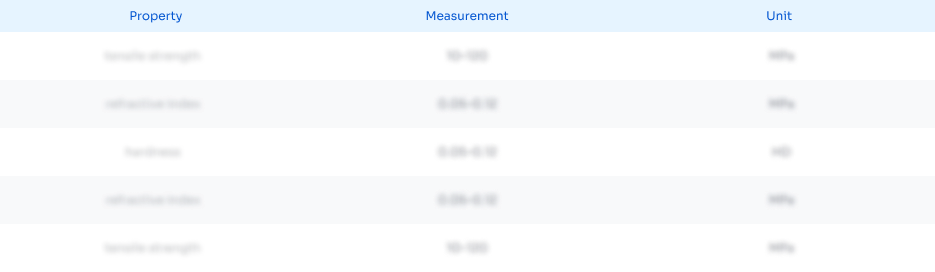
Abstract
Description
Claims
Application Information

- R&D Engineer
- R&D Manager
- IP Professional
- Industry Leading Data Capabilities
- Powerful AI technology
- Patent DNA Extraction
Browse by: Latest US Patents, China's latest patents, Technical Efficacy Thesaurus, Application Domain, Technology Topic, Popular Technical Reports.
© 2024 PatSnap. All rights reserved.Legal|Privacy policy|Modern Slavery Act Transparency Statement|Sitemap|About US| Contact US: help@patsnap.com