Multidimensional force sensor and calibration method thereof
A multi-dimensional force sensor and protector technology, applied in the field of sensors, can solve the problems of elastic properties change of elastomers, decrease in measurement accuracy, etc., and achieve the effect of protecting elastic columns
- Summary
- Abstract
- Description
- Claims
- Application Information
AI Technical Summary
Problems solved by technology
Method used
Image
Examples
Embodiment 1
[0061] Such as figure 1 As shown, the multidimensional force sensor of this embodiment includes an outer ring structure 1, an inner ring structure 2, an elastic column 3, a strain gauge and a protector 4; the outer ring structure 1 is circular, and the inner ring structure 2 has a structure of An equilateral triangle with rounded corners, the inner ring structure 2 and the outer ring structure 1 are connected by three elastic columns 3, and the two ends of each elastic column 3 are respectively connected to the outer ring structure 1 and the inner ring structure 2, and all the elastic columns 3 are evenly arranged around the central axis of the outer ring structure 1; the area where the inner ring structure 2 is in contact with the elastic column 3 is provided with long grooves 201, and each long groove 201 forms an edge-supported overhead plate on the surface of the inner ring structure 2 202 , the elastic column 3 is connected to the overhead plate 202 .
[0062] Such as ...
PUM
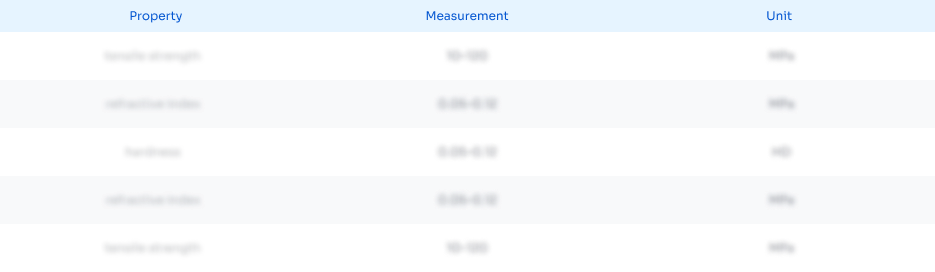
Abstract
Description
Claims
Application Information

- R&D
- Intellectual Property
- Life Sciences
- Materials
- Tech Scout
- Unparalleled Data Quality
- Higher Quality Content
- 60% Fewer Hallucinations
Browse by: Latest US Patents, China's latest patents, Technical Efficacy Thesaurus, Application Domain, Technology Topic, Popular Technical Reports.
© 2025 PatSnap. All rights reserved.Legal|Privacy policy|Modern Slavery Act Transparency Statement|Sitemap|About US| Contact US: help@patsnap.com