Low-power-action high-speed magnetic levitation vehicle suspension frame device
A low power, suspension frame technology, applied in the direction of electric vehicles, vehicle parts, electric traction, etc., can solve the problems of potential safety hazards, unfavorable suspension control, high manufacturing costs, etc., to facilitate installation and disassembly, facilitate suspension control, and improve suspension The effect of stability
- Summary
- Abstract
- Description
- Claims
- Application Information
AI Technical Summary
Problems solved by technology
Method used
Image
Examples
Embodiment Construction
[0023] The present invention will be further described below in conjunction with accompanying drawing and specific embodiment:
[0024] Such as figure 1 As shown, a kind of low dynamic effect high-speed maglev vehicle suspension frame device provided by the present invention includes a beam frame unit equipped with a secondary suspension system, and longitudinal beams are respectively installed on both sides of the two ends of the beam frame unit, and the ends of the longitudinal beams are A suspension frame unit is installed.
[0025] The beam frame unit includes a first beam 1, a second beam 2, a beam connector 3, an air spring mount 10 and a Z-shaped traction unit. The first beam 1 and the second beam 2 are arranged in parallel, and the beam connectors 3 are evenly distributed on the second beam. The first beam 1 and the second beam 2 are used for connecting the first beam 1 and the second beam 2 . The beam connectors 3 are located at both ends of the first beam 1 and the...
PUM
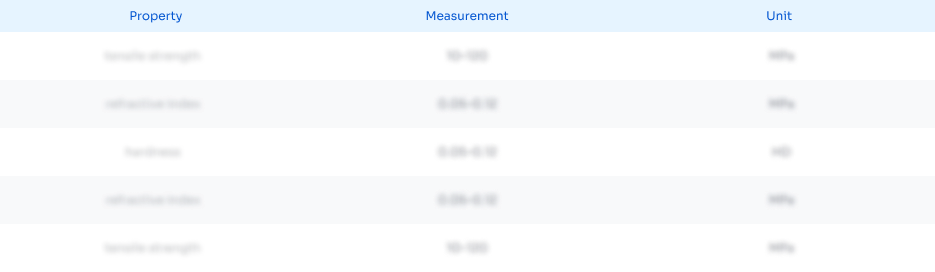
Abstract
Description
Claims
Application Information

- Generate Ideas
- Intellectual Property
- Life Sciences
- Materials
- Tech Scout
- Unparalleled Data Quality
- Higher Quality Content
- 60% Fewer Hallucinations
Browse by: Latest US Patents, China's latest patents, Technical Efficacy Thesaurus, Application Domain, Technology Topic, Popular Technical Reports.
© 2025 PatSnap. All rights reserved.Legal|Privacy policy|Modern Slavery Act Transparency Statement|Sitemap|About US| Contact US: help@patsnap.com