A hydraulic pipe joint vibration test device
A technology for hydraulic pipe joints and vibration testing, which is applied in vibration testing, measuring devices, and testing of machine/structural components. smooth effect
- Summary
- Abstract
- Description
- Claims
- Application Information
AI Technical Summary
Problems solved by technology
Method used
Image
Examples
Embodiment Construction
[0011] Below in conjunction with accompanying drawing and embodiment the patent of the present invention is further described.
[0012] Such as figure 1 As shown, a hydraulic pipe joint vibration test device includes a multi-cam disc (1), a fixed flange (2), a hydraulic motor (3), a base support (4), a spring structure support (5), a deep groove ball The bearing (6) and the tested piece (7) are characterized in that: the multi-cam disc (1) is fixed on the fixed flange (2) by standard bolts, and the fixed flange (2) is connected by standard bolts On the hydraulic motor (3), the hydraulic motor (3) is fixedly sleeved on the base bracket (4) through standard bolts, and the spring structure bracket (5) is fixed on the base bracket (4) through standard bolts, The deep groove ball bearing (6) is fixed on the steel pipe of the test piece (7) through interference fit, and the multi-cam disc (1) keeps in conflict with the deep groove ball bearing (6).
[0013] Such as figure 2 show...
PUM
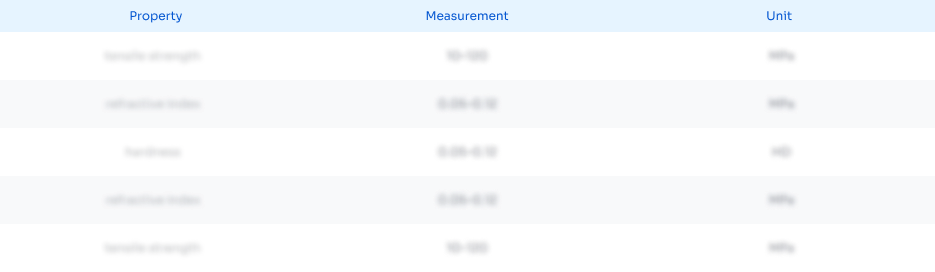
Abstract
Description
Claims
Application Information

- R&D
- Intellectual Property
- Life Sciences
- Materials
- Tech Scout
- Unparalleled Data Quality
- Higher Quality Content
- 60% Fewer Hallucinations
Browse by: Latest US Patents, China's latest patents, Technical Efficacy Thesaurus, Application Domain, Technology Topic, Popular Technical Reports.
© 2025 PatSnap. All rights reserved.Legal|Privacy policy|Modern Slavery Act Transparency Statement|Sitemap|About US| Contact US: help@patsnap.com