Bicycle rear tripod robot welding system
A robot welding and tripod technology, applied in welding equipment, auxiliary welding equipment, welding/cutting auxiliary equipment, etc., can solve the problems of high work intensity of operators, low welding efficiency, welding smoke and arc light human hazards, etc., to reduce the number of back and forth The effect of walking time, improving use efficiency and ensuring appearance quality
- Summary
- Abstract
- Description
- Claims
- Application Information
AI Technical Summary
Problems solved by technology
Method used
Image
Examples
Embodiment 1
[0028] Such as figure 1 , 4 As shown, a bicycle rear tripod robot welding system includes a base 2, a station switch positioner 3 is arranged on the base 2, and two-axis positioners are respectively connected to the two sides of the station switch positioner 3 5. The biaxial positioner 5 is connected with a rear tripod welding jig 4, the base 2 is provided with a welding robot 1 on one side of one of the rear tripod welding jigs 4, and a welding robot 1 is provided on one side of the base 2 for The robot control cabinet 7 that controls the welding robot 1, the station switching and turning positioner 3 and the biaxial positioner 5.
[0029] The welding system of this embodiment adopts a dual-station design. By opening the robot control cabinet 7, the two-axis positioner 5 is switched by relying on the station switching and turning positioner 3, so that the switching of the stations is realized, and the operator's operation time is reduced. The back and forth travel time when...
Embodiment 2
[0031] Such as Figure 2~3 As shown, the rear tripod welding fixture in the first embodiment includes a station base 4-10, and the station base 4-10 is respectively provided with a locking plate positioning mechanism 4-3 for positioning the rear tripod locking plate 204, The upper fork tube positioning mechanism 4-2 for positioning the rear tripod upper fork tube 205, the rear fork sheet pressing mechanism 4-1 for positioning the rear tripod rear fork 206, and the lower fork for positioning the rear tripod lower fork tube 203 Tube positioning mechanism 4-7, the standpipe positioning and pressing mechanism 4-4 for positioning the rear tripod standpipe 202, the bottom bracket positioning mechanism 4-5 for positioning the rear tripod bottom bracket tube 201, the bottom bracket positioning mechanism Positioning pins 4-6 are arranged on both sides of the 4-5, and a water-cooling circuit is arranged in the positioning pins 4-6 and the rear fork pressing mechanism 4-1.
[0032] The ...
Embodiment 3
[0035] A baffle 6 is provided in the center of the station switching and turning positioner 3, which can effectively prevent arc light and smoke pollution.
PUM
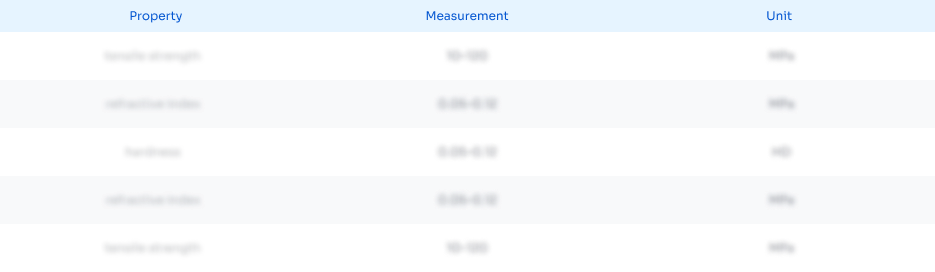
Abstract
Description
Claims
Application Information

- R&D
- Intellectual Property
- Life Sciences
- Materials
- Tech Scout
- Unparalleled Data Quality
- Higher Quality Content
- 60% Fewer Hallucinations
Browse by: Latest US Patents, China's latest patents, Technical Efficacy Thesaurus, Application Domain, Technology Topic, Popular Technical Reports.
© 2025 PatSnap. All rights reserved.Legal|Privacy policy|Modern Slavery Act Transparency Statement|Sitemap|About US| Contact US: help@patsnap.com