A High Precision Fiber Bragg Grating Deformation Sensor Based on Curved Triangle
A technology of deformation sensors and curved triangles, applied in instruments, optical devices, measuring devices, etc., can solve problems such as being susceptible to electromagnetic interference, difficult to remove zero point drift, and limiting ground stress detection, etc., to achieve easy wavelength division multiplexing, Not easy to electromagnetic interference, zero drift convenient effect
- Summary
- Abstract
- Description
- Claims
- Application Information
AI Technical Summary
Problems solved by technology
Method used
Image
Examples
Embodiment Construction
[0023] The technical solutions in the embodiments of the present invention will be clearly and completely described below in conjunction with the accompanying drawings in the embodiments of the present invention. Obviously, the described embodiments are only some of the embodiments of the present invention, not all of them. Based on the embodiments of the present invention, all other embodiments obtained by persons of ordinary skill in the art without making creative efforts belong to the protection scope of the present invention.
[0024] Embodiments of the present invention will be further described in detail below in conjunction with the accompanying drawings.
[0025] Such as figure 1 and figure 2 As shown, a high-precision fiber grating deformation sensor based on a curved triangle is used to measure the stress-strain state of the crust in seismic observation, including: a closed stainless steel outer cylinder, a triangular copper plate 1, a vertical metal rod 2 and a h...
PUM
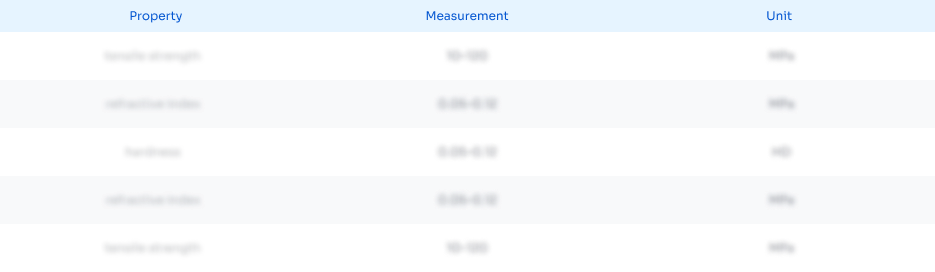
Abstract
Description
Claims
Application Information

- R&D Engineer
- R&D Manager
- IP Professional
- Industry Leading Data Capabilities
- Powerful AI technology
- Patent DNA Extraction
Browse by: Latest US Patents, China's latest patents, Technical Efficacy Thesaurus, Application Domain, Technology Topic, Popular Technical Reports.
© 2024 PatSnap. All rights reserved.Legal|Privacy policy|Modern Slavery Act Transparency Statement|Sitemap|About US| Contact US: help@patsnap.com