Granular bed filtering dust removal system
A particle bed filtration and dust removal system technology, which is applied in the direction of dispersed particle separation, separation methods, chemical instruments and methods, etc., can solve the problems that affect the settlement and discharge of fine dust, the difficulty of preventing tar and dust accumulation, and the inability to accept back blowing gas, etc. , to achieve the effect of promoting dust settlement, stable work with little impact, and efficient and reliable removal
- Summary
- Abstract
- Description
- Claims
- Application Information
AI Technical Summary
Problems solved by technology
Method used
Image
Examples
Embodiment 1
[0031] A kind of particle bed filter dust removal system that present embodiment proposes, such as figure 1 As shown, it includes three main particle bed filter dust collectors 1, a secondary particle bed filter dust collector 2, dusty gas main pipe 3, clean gas main pipe 4 and back blowing gas main pipe 5, and a main particle bed filter dust collector 1 There are six layers, two in each layer, and a total of twelve primary particle beds 11. The top of the primary particle bed filter and dust collector 1 is connected to the dust-containing gas main pipe 3, specifically, the dust-containing gas main pipe 3 is connected in series with the main dust-containing gas main pipe 3. The main dust-containing air inlet branch pipe 32 of the intake valve 31 is connected with the top of the main particle bed filter dust collector 1, and the dust-containing gas main pipe 3 transports the dust-containing gas to the main particle bed filter dust collector 1, and the main particle bed filter du...
Embodiment 2
[0040] A kind of particle bed filter dust removal system that present embodiment proposes, such as figure 2 As shown, it is basically the same structure as the particle bed filter and dust removal system of Embodiment 1, the difference is only: the upstream of the reverse blowing air main pipe 5 is connected with a reverse blower 91, and the inlet end of the reverse blower 91 feeds clean gas. During processing, the inlet end of the reverse blower 91 communicates with the outlet end of the external clean air induced draft fan (not shown) or communicates with the external clean air gas cabinet to feed clean air, and the outlet end of the reverse blower 91 connects with the reverse blow air main pipe A mixer 93 for mixing clean gas and high-temperature flue gas is provided between the inlet ends of the gas inlet 5, and the mixer 93 is connected to a burner 94 that provides high-temperature flue gas, and the low-temperature clean gas is raised to back blowing by mixing high-temper...
Embodiment 3
[0043] A kind of particle bed filter dust removal system that present embodiment proposes, such as image 3 As shown, it is basically the same as the structure of the particle bed filter and dust removal system of embodiment one or the structure of the particle bed filter and dust removal system of embodiment two, the only difference is: the upstream of the back blowing air main pipe 5 is connected with a reverse blower 91, The inlet end of the reverse blower 91 is fed with high-temperature flue gas. In actual processing, the inlet end of the reverse blower 91 is connected with the high-temperature flue gas pipeline (not shown in the figure), and the high-temperature flue gas is directly introduced to meet the temperature requirements of the reverse blower. The high-temperature flue gas is used as the blowback gas. The outlet end of the dust-laden back-blowing gas outlet pipe 81 is connected in series with the outlet valve 82 and connected to the dust-laden gas main pipe 3. Wh...
PUM
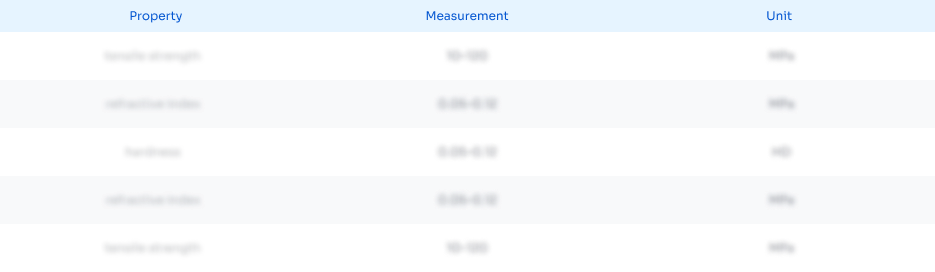
Abstract
Description
Claims
Application Information

- R&D
- Intellectual Property
- Life Sciences
- Materials
- Tech Scout
- Unparalleled Data Quality
- Higher Quality Content
- 60% Fewer Hallucinations
Browse by: Latest US Patents, China's latest patents, Technical Efficacy Thesaurus, Application Domain, Technology Topic, Popular Technical Reports.
© 2025 PatSnap. All rights reserved.Legal|Privacy policy|Modern Slavery Act Transparency Statement|Sitemap|About US| Contact US: help@patsnap.com