Three-finger-three-knuckle under-actuated mechanical arm with finger tail end path being controllable
An underactuated and manipulator technology, which is applied in the direction of program-controlled manipulators, manipulators, chucks, etc., can solve the problems of uncertain movement of finger end trajectory, loss of finger flexibility, etc., achieve convenient and fast disassembly and installation, improve grasping flexibility, and structure and the effect of simple principle
- Summary
- Abstract
- Description
- Claims
- Application Information
AI Technical Summary
Problems solved by technology
Method used
Image
Examples
specific Embodiment approach 1
[0044] Specific implementation mode one: combine Figure 1 to Figure 16 Describe this embodiment. This embodiment includes three underactuated fingers, an underactuated manipulator base 70, a finger rotating motor 71, a driving gear 72, a first driven gear 73, and a second driven gear 74. The three underactuated fingers form a triangular row. cloth, each underactuated finger includes a power drive part and a joint part, the joint part is connected to the output end of the power drive part, and the joint part includes a first joint 8, a second joint 9, a third joint 10, a guide wheel mechanism, a reset Mechanism and locking mechanism, the first joint 8, the second joint 9 and the third joint 10 are rotatably connected in turn, and the guide wheel mechanism, reset mechanism and locking mechanism are installed on the first joint 8, the second joint 9 and the third joint On the joint 10, the guide wheel mechanism is driven by the power drive part to realize the grasping action of ...
specific Embodiment approach 2
[0049] Specific implementation mode two: combination Figure 9 , Figure 11 and Figure 14 Describe this embodiment. This embodiment also includes a plurality of bearings 75 and a cover body 76. The plurality of bearings 75 are respectively set on the fixed sleeve 3 at the upper end of the first driven gear 73 and the second driven gear 74. The cover body 76 covers On the entire powered portion of the underactuated manipulator base 70 outside. With such arrangement, it is convenient to ensure that two adjacent fingers rotate smoothly in the same or opposite direction. Other compositions and connections are the same as in the first embodiment.
[0050] When the motor 1 has no output, the underactuated mechanical finger will return to the initial state under the action of the joint return spring and the mechanical limit (at this time, the entire finger is in a horizontal state, and the other components are the motor 1, the connecting sleeve 2, and the fixing sleeve 3 and fin...
specific Embodiment approach 3
[0051] Specific implementation mode three: combination Figure 5 Describe this embodiment, the power drive part of this embodiment also includes tightening wheel cover 18 and idler bracket 19, tightening wheel cover 18 is installed in the connecting sleeve 2 and is sleeved on the output shaft of motor 1, and idler bracket 19 Installed on the connecting sleeve 2, the second guide wheel 17 partially extends into the fixed sleeve 3, and the first guide wheel 6 and the second guide wheel 7 are all installed on the guide wheel bracket 19. In this way, the tightening wheel cover 18 and the winding wheel are fixed on the output shaft of the motor through screws, the motor is fixed on the connecting sleeve through screws, the guide wheel bracket is fixed on the connecting sleeve through screws, and the connecting sleeve is connected through screws. This part is integrally fixed on the base, so that the connection between the motor and other components is more compact. Other compositi...
PUM
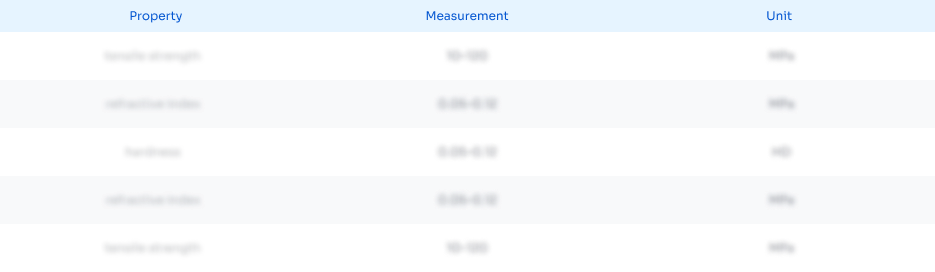
Abstract
Description
Claims
Application Information

- R&D
- Intellectual Property
- Life Sciences
- Materials
- Tech Scout
- Unparalleled Data Quality
- Higher Quality Content
- 60% Fewer Hallucinations
Browse by: Latest US Patents, China's latest patents, Technical Efficacy Thesaurus, Application Domain, Technology Topic, Popular Technical Reports.
© 2025 PatSnap. All rights reserved.Legal|Privacy policy|Modern Slavery Act Transparency Statement|Sitemap|About US| Contact US: help@patsnap.com