The method of self-checking and returning to zero of the stepping motor motion system
A stepper motor and motion system technology, applied in the control system, motor generator control, electrical components, etc., can solve the problems of affecting the speed and efficiency of zero return, poor zero return accuracy, unusable, etc., to achieve fast and reliable Self-check back to zero, simplify the debugging process and debugging program, reduce the effect of idle travel
- Summary
- Abstract
- Description
- Claims
- Application Information
AI Technical Summary
Problems solved by technology
Method used
Image
Examples
Embodiment 1
[0055] like Figure 1-2 As shown, this embodiment provides a method for self-checking and returning to zero of the stepping motor motion system, which means that the stepping motor starts from any zero-returning starting position Pr, combines and switches between slow speed and fast speed, and only moves toward one Direction movement finds the global zero point P0, and corrects it to the true zero point Pa, and completes the method of self-checking and returning to zero; the specific steps are as follows:
[0056] (1) The stepper motor moves towards the global zero point P0 starting from any zero-return starting position Pr;
[0057] (2) During the motion process, when moving towards the global zero point P0 at a constant speed at a slower speed Vs, the slow motion distance exceeds the distance from the true zero point Pa to the global zero point P0, and then accelerates;
[0058] During the movement, when moving towards the global zero point P0 at a faster speed Vq at a unif...
PUM
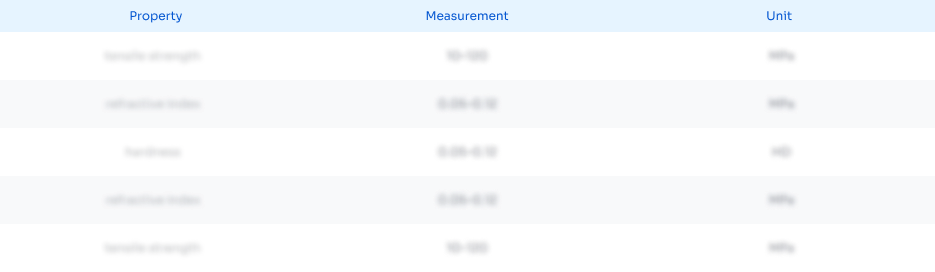
Abstract
Description
Claims
Application Information

- R&D Engineer
- R&D Manager
- IP Professional
- Industry Leading Data Capabilities
- Powerful AI technology
- Patent DNA Extraction
Browse by: Latest US Patents, China's latest patents, Technical Efficacy Thesaurus, Application Domain, Technology Topic, Popular Technical Reports.
© 2024 PatSnap. All rights reserved.Legal|Privacy policy|Modern Slavery Act Transparency Statement|Sitemap|About US| Contact US: help@patsnap.com