Digital rate integrating gyroscope control method based on parametric excitation and platform
A technology of parameter excitation and control method, which is applied in the direction of speed measurement by gyro effect, gyroscope/steering sensing equipment, measuring device, etc., and can solve problems such as error, rate integration mode failure, drive component error circuit, etc.
- Summary
- Abstract
- Description
- Claims
- Application Information
AI Technical Summary
Problems solved by technology
Method used
Image
Examples
Embodiment Construction
[0064] The present invention will be described in detail below in conjunction with the accompanying drawings and embodiments.
[0065] Such as figure 1 As shown, the control method and platform of the present invention are applicable to the biaxially symmetrical Coriolis vibrating gyro structure, and of course can also be applied to other Coriolis vibrating gyro structures. The biaxially symmetrical Coriolis vibrating gyroscope has two moving directions of the X axis and the Y axis, and the detection parts, the driving device and the parameter driving device are respectively arranged in the X axis and the Y axis moving directions; the detection parts are used to detect the X axis respectively. and Y-axis motion displacement and converted into X-axis and Y-axis motion output voltage, respectively applying a driving voltage to the drive device in the X-axis and / or Y-axis motion direction will apply a motion along the X-axis and / or Y-axis to the vibrating gyroscope The driving f...
PUM
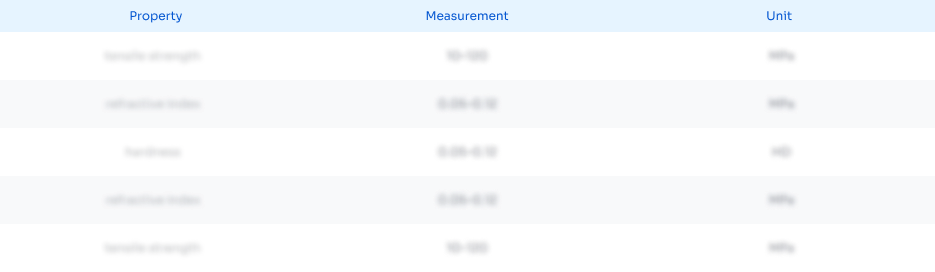
Abstract
Description
Claims
Application Information

- Generate Ideas
- Intellectual Property
- Life Sciences
- Materials
- Tech Scout
- Unparalleled Data Quality
- Higher Quality Content
- 60% Fewer Hallucinations
Browse by: Latest US Patents, China's latest patents, Technical Efficacy Thesaurus, Application Domain, Technology Topic, Popular Technical Reports.
© 2025 PatSnap. All rights reserved.Legal|Privacy policy|Modern Slavery Act Transparency Statement|Sitemap|About US| Contact US: help@patsnap.com