Bridge monitoring equipment
A technology for monitoring equipment and bridges, applied in mechanical equipment, supporting machines, machines/brackets, etc., can solve the problems of cumbersome disassembly and assembly process, time-consuming and labor-intensive efficiency, affecting normal work, etc., to reduce operation steps and improve installation. Speed, effect of preventing accidental electric shock
- Summary
- Abstract
- Description
- Claims
- Application Information
AI Technical Summary
Problems solved by technology
Method used
Image
Examples
Embodiment Construction
[0018] Such as Figure 1-Figure 6 As shown, a bridge monitoring device of the present invention includes a top base 7 and an insertion portion 8, the right side of the top base 7 is provided with a pillar 10, and the bottom of the pillar 10 is fixedly provided with a support seat 101, and the pillar 10 is provided with a strut 102 on the left side of the upper end, and the end of the strut 102 away from the strut 10 is fixedly connected with the right end surface of the top seat 7, and the top seat 7 is provided with a cavity 71, the cavity The inner top wall of cavity 71 is provided with spring insertion hole 72, and the inner top wall of described cavity 71 on both sides of described insertion spring hole 72 is provided with first motor 73 commensurately, each described first motor 73 bottoms Both are connected with a first screw rod 74, and the first screw rod 74 is threadedly connected with an assembly block 9, and the middle end of the assembly block 9 is provided with an...
PUM
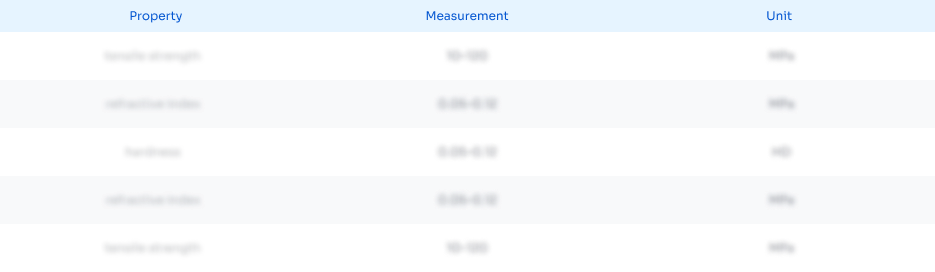
Abstract
Description
Claims
Application Information

- R&D Engineer
- R&D Manager
- IP Professional
- Industry Leading Data Capabilities
- Powerful AI technology
- Patent DNA Extraction
Browse by: Latest US Patents, China's latest patents, Technical Efficacy Thesaurus, Application Domain, Technology Topic, Popular Technical Reports.
© 2024 PatSnap. All rights reserved.Legal|Privacy policy|Modern Slavery Act Transparency Statement|Sitemap|About US| Contact US: help@patsnap.com