Coordinate calibration method for micro-injection system on basis of robot assistance
A robot-assisted microinjection technology, which is applied in the direction of hypodermic injection devices, can solve the problem of low efficiency of needle point movement and positioning, and achieve the effect of improving work efficiency and high measurement accuracy
- Summary
- Abstract
- Description
- Claims
- Application Information
AI Technical Summary
Problems solved by technology
Method used
Image
Examples
specific Embodiment approach 1
[0030] The coordinate calibration method of the robot-assisted microinjection system of the present embodiment, such as Figure 5 As shown, the method is realized through the following steps:
[0031] Step 1: Set the coordinate system of the microscope stage as O s -X s Y s Z s , origin O s is the initial position; the camera coordinate system is O c -X c Y c Z c , point O c Located in the center of the objective lens of the microscope, Z c is the optical axis of the microscope; the coordinate system of the three-degree-of-freedom manipulator is O m -X m Y m Z m ; The coordinate system of the calibration bitmap image plane is O i -UV, origin O i in the upper left corner of the image; and make sure:
[0032] The coordinate transformation matrix between the three-degree-of-freedom manipulator coordinate system and the camera coordinate system is Then the conversion relationship between the three-degree-of-freedom manipulator coordinate system and the camera coo...
specific Embodiment approach 2
[0048] The difference from the specific embodiment 1 is that the coordinate calibration method of the robot-assisted microinjection system in this embodiment is determined as described in step 1:
[0049] The coordinate transformation matrix between the three-degree-of-freedom manipulator coordinate system and the camera coordinate system is Then the conversion relationship between the three-degree-of-freedom manipulator coordinate system and the camera coordinate system is:
[0050] The coordinate transformation matrix between the calibration bitmap image plane coordinate system and the camera coordinate system is Then the conversion relationship between the calibration bitmap image plane coordinate system and the camera coordinate system is: as well as
[0051] The coordinate transformation matrix between the three-degree-of-freedom manipulator coordinate system and the calibration bitmap image plane coordinate system is Then the conversion relationship between the ...
specific Embodiment approach 3
[0060] The difference from Embodiment 1 or Embodiment 2 is that in the coordinate calibration method of the robot-assisted microinjection system in this embodiment, the process of calculating the time for the mechanical arm to complete movement in the field of view described in step 2 is as follows: When moving between two adjacent horizontal, vertical or oblique calibration points in the field of view, the moving distances in the direction of the horizontal u-axis and the longitudinal v-axis are Δx and Δy respectively, and the points in the field of view The array has n in the direction of the horizontal u-axis and the vertical v-axis respectively 1 and n 2 points, such as Figure 4 shown, and
[0061] Horizontal u-axis direction, such as calibration point 1→2, the mechanical arm between two adjacent points is at x m 、y m ,z m The distance to move in each direction:
[0062] x m = Δy cos γ, y m = Δy sin γ, z m =Δy cosγtanα;
[0063] Longitudinal v-axis direction, su...
PUM
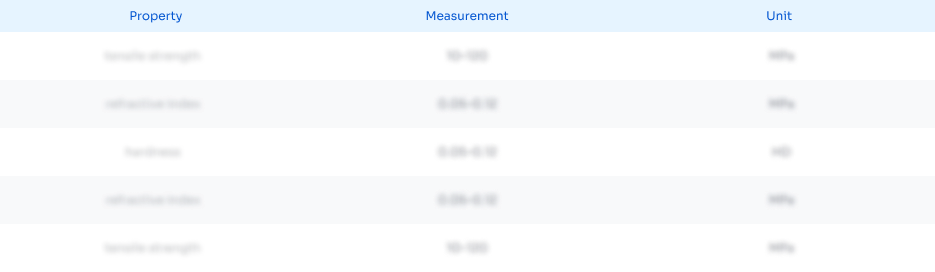
Abstract
Description
Claims
Application Information

- R&D
- Intellectual Property
- Life Sciences
- Materials
- Tech Scout
- Unparalleled Data Quality
- Higher Quality Content
- 60% Fewer Hallucinations
Browse by: Latest US Patents, China's latest patents, Technical Efficacy Thesaurus, Application Domain, Technology Topic, Popular Technical Reports.
© 2025 PatSnap. All rights reserved.Legal|Privacy policy|Modern Slavery Act Transparency Statement|Sitemap|About US| Contact US: help@patsnap.com