Automatic spraying system coordinate transform method based on point cloud and image matching
A technology of automatic spraying and coordinate transformation, applied in image analysis, image enhancement, image data processing, etc., can solve the problems of long time, large working space, low efficiency, etc.
- Summary
- Abstract
- Description
- Claims
- Application Information
AI Technical Summary
Problems solved by technology
Method used
Image
Examples
Embodiment Construction
[0061] figure 1 It is a flowchart of the present invention, as shown in the figure, a method for coordinate transformation of an automated spraying system based on point cloud and image matching provided by the present invention, including:
[0062] S1. Construct the robot coordinate system R, the image coordinate system U and the point cloud coordinate system V, and the X-Y planes of the robot coordinate system R, the image coordinate system U and the point cloud coordinate system V are parallel to each other;
[0063] S2. Collect the image Q of the spraying object on the spraying platform, and obtain the description of the spraying object in the robot coordinate system R: R Q= R T U U Q; where, R Q is the description of the image Q in the robot coordinate system R, U Q is the description of the image Q in the image coordinate system U, R T U is the transformation from the image coordinate system U to the robot coordinate system;
[0064] S3. Obtain the geometric prop...
PUM
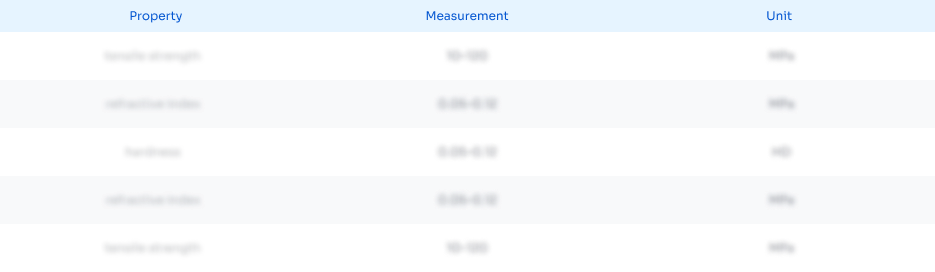
Abstract
Description
Claims
Application Information

- R&D
- Intellectual Property
- Life Sciences
- Materials
- Tech Scout
- Unparalleled Data Quality
- Higher Quality Content
- 60% Fewer Hallucinations
Browse by: Latest US Patents, China's latest patents, Technical Efficacy Thesaurus, Application Domain, Technology Topic, Popular Technical Reports.
© 2025 PatSnap. All rights reserved.Legal|Privacy policy|Modern Slavery Act Transparency Statement|Sitemap|About US| Contact US: help@patsnap.com