Axial plunger pump flow distribution pair test oil membrane thickness test system
An axial piston pump and testing system technology, applied in the field of liquid pumps, can solve the problems of difficult sensor arrangement and installation, inability to completely simulate the working conditions of the real pump, and restricting the performance and life of the axial piston pump.
- Summary
- Abstract
- Description
- Claims
- Application Information
AI Technical Summary
Problems solved by technology
Method used
Image
Examples
Embodiment Construction
[0022] The present invention will be further described in detail below in conjunction with the accompanying drawings and specific embodiments.
[0023] Such as figure 2 As shown, this technical solution is a subsystem of the axial piston pump distribution pair test bench, and the axial piston pump distribution pair test bench includes the drive motor 15, data acquisition and control assembly, hydraulic assembly, and distribution pair oil film thickness Test system; except for the oil film thickness test system of the distribution sub-assembly, other assemblies are existing technologies. This technical solution only describes the structure and control related to it, and the others will not be described in detail. The data acquisition and control assembly comprises the rotational speed torque sensor 26 installed on the output end of the drive motor 15, the rotational speed torque console for controlling the drive motor 15, the data acquisition module for receiving the rotationa...
PUM
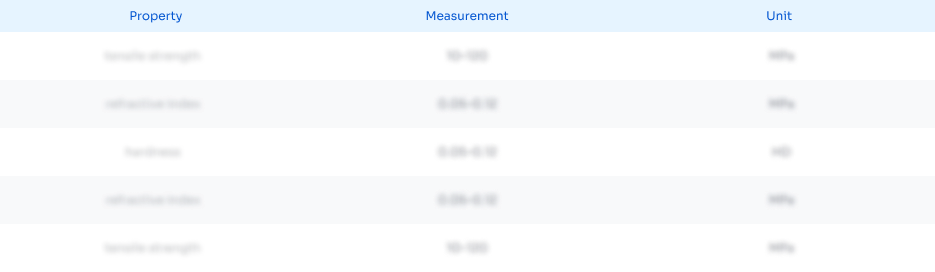
Abstract
Description
Claims
Application Information

- Generate Ideas
- Intellectual Property
- Life Sciences
- Materials
- Tech Scout
- Unparalleled Data Quality
- Higher Quality Content
- 60% Fewer Hallucinations
Browse by: Latest US Patents, China's latest patents, Technical Efficacy Thesaurus, Application Domain, Technology Topic, Popular Technical Reports.
© 2025 PatSnap. All rights reserved.Legal|Privacy policy|Modern Slavery Act Transparency Statement|Sitemap|About US| Contact US: help@patsnap.com