Desulfurizing smelting method for ultra low sulfur pure iron
A smelting method and ultra-low sulfur technology, applied in the field of iron and steel smelting, can solve problems such as flammability and explosion, endangering safety, storage and transportation losses, etc.
- Summary
- Abstract
- Description
- Claims
- Application Information
AI Technical Summary
Problems solved by technology
Method used
Image
Examples
Embodiment 1
[0040] 1.1. EAF process requirements:
[0041] Electric furnace tapping requirements: [P]0.000~0.005%, [Si]0.00~0.50%;
[0042] After Si and P meet the above requirements, carry out complete slag removal, and then tap;
[0043]Tapping at the bottom of the eccentric furnace, during the tapping process, add: deoxidizer aluminum ingot 1.5~2.5kg / t;
[0044] 1.2. Process requirements of LF furnace
[0045] LF furnace slagging deoxidation and desulfurization uses fluorite, dry activated lime and calcium carbide to mix to obtain slag as a weight percentage. The components are: CaO: 55-75%; CaF 2 : 10~25%; CaC 2 : 10~20%;
[0046] Before the LF furnace hangs the bag to the VD furnace [S] to 0.000~0.001%;
[0047] 1.3, VD furnace process requirements
[0048] VD is vacuum degassed;
[0049] After the vacuum treatment is completed, the temperature is measured and sampled, and the composition is controlled according to the aforementioned requirements according to the analysis resu...
PUM
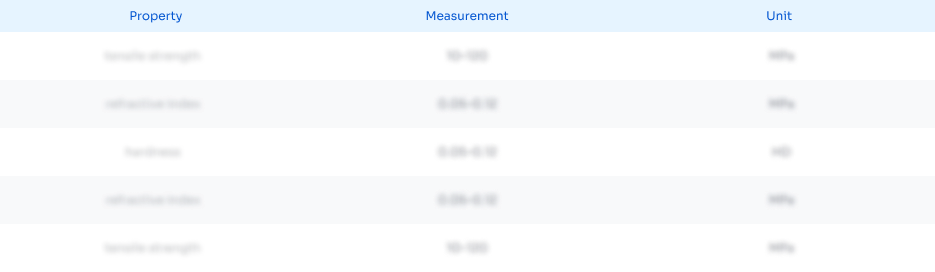
Abstract
Description
Claims
Application Information

- R&D Engineer
- R&D Manager
- IP Professional
- Industry Leading Data Capabilities
- Powerful AI technology
- Patent DNA Extraction
Browse by: Latest US Patents, China's latest patents, Technical Efficacy Thesaurus, Application Domain, Technology Topic, Popular Technical Reports.
© 2024 PatSnap. All rights reserved.Legal|Privacy policy|Modern Slavery Act Transparency Statement|Sitemap|About US| Contact US: help@patsnap.com