Tilting wing UAV with an aerodynamic layout and tilting mechanism
A technology of tilting mechanism and tilting wings, applied in the field of unmanned aerial vehicles, can solve the problems of fast flight speed, high take-off site requirements, slow cruising speed, etc., and achieve the effects of long battery life, high force-to-efficiency ratio and high efficiency
- Summary
- Abstract
- Description
- Claims
- Application Information
AI Technical Summary
Problems solved by technology
Method used
Image
Examples
Embodiment Construction
[0024] Aiming at the above-mentioned technical solution, a preferred embodiment is given and described in detail with reference to the drawings. see Figure 1 to Figure 5 , the present invention includes a fuselage, a front wing, a rear wing, a propeller power unit, a tilting mechanism, wherein.
[0025] Before and after the fuselage 1, a front rotating shaft 11 and a rear rotating shaft 12 are installed, and the front rotating shaft and the rear rotating shaft run through the fuselage transversely respectively, so that the two ends of the front and rear rotating shafts are respectively located at both sides of the fuselage. Both sides in the fuselage where front and rear rotating shafts are provided with support bearing housing 13, are used for supporting front rotating shaft and rear rotating shaft, make front rotating shaft and rear rotating shaft can rotate under the support of bearing housing. In the fuselage, the installation height of the front rotating shaft is lower ...
PUM
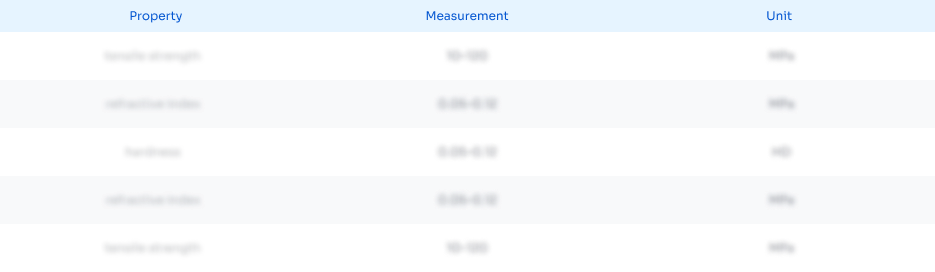
Abstract
Description
Claims
Application Information

- R&D
- Intellectual Property
- Life Sciences
- Materials
- Tech Scout
- Unparalleled Data Quality
- Higher Quality Content
- 60% Fewer Hallucinations
Browse by: Latest US Patents, China's latest patents, Technical Efficacy Thesaurus, Application Domain, Technology Topic, Popular Technical Reports.
© 2025 PatSnap. All rights reserved.Legal|Privacy policy|Modern Slavery Act Transparency Statement|Sitemap|About US| Contact US: help@patsnap.com