Stud welding error preventing mechanism
A stud welding, error-proof technology, applied in welding equipment, welding accessories, arc welding equipment, etc., to achieve the effect of high work efficiency, simple structure and convenient operation
- Summary
- Abstract
- Description
- Claims
- Application Information
AI Technical Summary
Problems solved by technology
Method used
Image
Examples
Embodiment 1
[0023] As a preferred embodiment, such as Figure 4 As shown, the rotation fulcrum 30 of the error-proof cover 3 is set on the opening edge of the stud guide sleeve 2, and the error-proof cover 3 is provided with a handle 31 for pulling the error-proof cover 3 to rotate. The worker manually pulls the handle 31 to drive the error-proofing cover 3 to rotate to the opening of the stud guide sleeve 2 to complete simple and reliable manual operation to complete the error-proofing of the stud welding. Preferably, the error-proof cover plate 3 is a circular plate adapted to the shape of the opening of the stud guide sleeve 2, and the handle 31 and the rotation fulcrum 30 are respectively arranged at both ends of the same diameter of the circular plate. Such a structure not only realizes stud welding error-proofing through the error-proof cover plate 3 that can completely cover the opening of the stud guide cylinder 2, and avoids the magnetic force leaking out of the stud welding gun ...
Embodiment 2
[0025] As another preferred embodiment, such as Figure 5 , 6 As shown, the error-proof cover plate 3 is connected to the rotary cylinder 5 , and the rotating shaft 51 of the rotary cylinder 5 is parallel to the axial direction of the stud guide sleeve 2 . This embodiment is for automatic operation and error prevention. In actual use, only the assembly and movement space of the rotary cylinder needs to be reserved on the traditional stud welding guide mechanism 1, and the error prevention cover 3 is fixedly connected with the rotating shaft 51 of the rotary cylinder 51. , and then control the rotation of the rotary cylinder 5 through an integrated circuit, and control the rotation of the rotary cylinder 5 arranged at a station that does not require stud welding according to the difference of the vehicle type, and drive the error-proof cover 3 to block the opening of the stud guide sleeve 2 At this point, automatic stud welding error prevention can be completed. This kind of ...
PUM
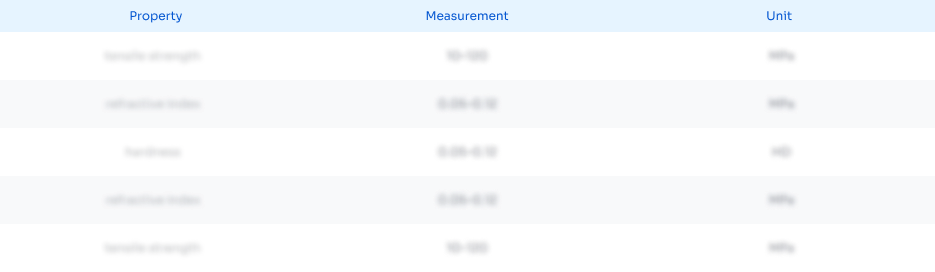
Abstract
Description
Claims
Application Information

- Generate Ideas
- Intellectual Property
- Life Sciences
- Materials
- Tech Scout
- Unparalleled Data Quality
- Higher Quality Content
- 60% Fewer Hallucinations
Browse by: Latest US Patents, China's latest patents, Technical Efficacy Thesaurus, Application Domain, Technology Topic, Popular Technical Reports.
© 2025 PatSnap. All rights reserved.Legal|Privacy policy|Modern Slavery Act Transparency Statement|Sitemap|About US| Contact US: help@patsnap.com