3D printer temperature control system
A technology of temperature control system and 3D printer, applied in temperature control using analog comparator, temperature control using electric mode, etc., can solve problems such as increasing CPU workload, response conflict, program running away, etc., to achieve beneficial functions The effect of scaling, reducing CPU load, and improving real-time performance
- Summary
- Abstract
- Description
- Claims
- Application Information
AI Technical Summary
Problems solved by technology
Method used
Image
Examples
Embodiment Construction
[0046] The present invention will be further described below in conjunction with the accompanying drawings and examples.
[0047] figure 2 It is a schematic diagram of the hardware structure of the temperature control system of the 3D printer according to the embodiment of the present invention. The temperature control system includes a bus interface module, a register file, a PID calculation module (including a print head PID calculation module and a hot bed PID calculation module) and a temperature acquisition module, which are connected in sequence. The print head PID calculation module and the hot bed PID calculation module are also connected respectively. Print head heating module and hot bed heating module. If the temperature collected by the temperature collection module does not exceed the preset range, the temperature data of the print head and the hot bed are sent to the PID operation module. After the calculation of the PID operation module is completed, it will ...
PUM
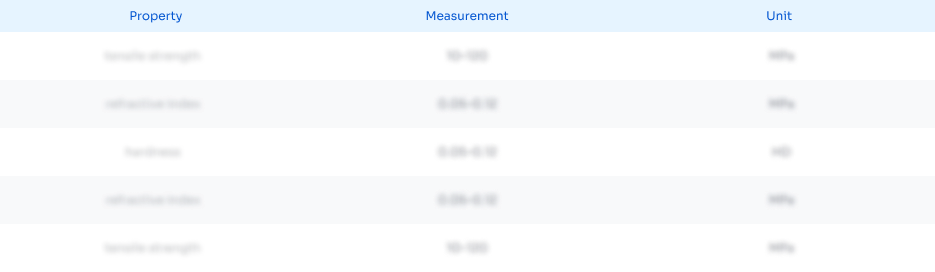
Abstract
Description
Claims
Application Information

- Generate Ideas
- Intellectual Property
- Life Sciences
- Materials
- Tech Scout
- Unparalleled Data Quality
- Higher Quality Content
- 60% Fewer Hallucinations
Browse by: Latest US Patents, China's latest patents, Technical Efficacy Thesaurus, Application Domain, Technology Topic, Popular Technical Reports.
© 2025 PatSnap. All rights reserved.Legal|Privacy policy|Modern Slavery Act Transparency Statement|Sitemap|About US| Contact US: help@patsnap.com