Robot vehicle body suspension system
A suspension system and robot technology, applied in suspension, elastic suspension, vehicle components, etc., can solve the problems of poor robot stability and low utilization rate of frame structure strength, and achieve reliable performance, simple structure, and strong environmental adaptability. Effect
- Summary
- Abstract
- Description
- Claims
- Application Information
AI Technical Summary
Problems solved by technology
Method used
Image
Examples
Embodiment Construction
[0022] The present invention will be further described below in conjunction with accompanying drawing and specific embodiment:
[0023] Such as Figure 1-6 As shown, the robot car body suspension system of the present invention includes a suspension mechanism 1, a coupling mechanism 2, a motor 3, a driver (not shown in the figure) and wheels 4, and the suspension mechanism 1 includes a support frame 11, a connecting rod assembly, a transverse Arm assembly and shock absorber 12, support frame 11 and connecting rod assembly, cross arm assembly form double parallelogram mechanism, shock absorber 12 is positioned between double parallelogram mechanism and is vertical direction its two ends respectively connect support frame 11 and As for the connecting rod assembly, the motor 3 is arranged at the bottom of the suspension mechanism 1, and is connected with the wheel 4 through the coupling mechanism 2, and the driver is clamped on the motor 3 and connected to the motor circuit.
[...
PUM
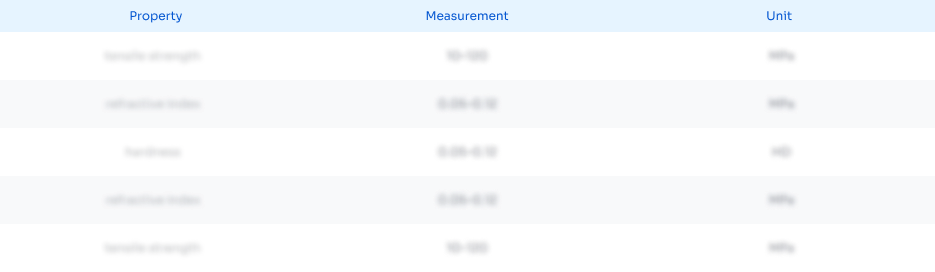
Abstract
Description
Claims
Application Information

- Generate Ideas
- Intellectual Property
- Life Sciences
- Materials
- Tech Scout
- Unparalleled Data Quality
- Higher Quality Content
- 60% Fewer Hallucinations
Browse by: Latest US Patents, China's latest patents, Technical Efficacy Thesaurus, Application Domain, Technology Topic, Popular Technical Reports.
© 2025 PatSnap. All rights reserved.Legal|Privacy policy|Modern Slavery Act Transparency Statement|Sitemap|About US| Contact US: help@patsnap.com