Plug-in electrical connector press-in nut structure
An electrical connector, plug-in technology, applied in the field of improved structure of the plug-in electrical connector pressing into the nut, can solve the problems of enhanced torque and pull-out force requirements, complex processing technology, limited torque and tension, etc. The effect of pull-out force
- Summary
- Abstract
- Description
- Claims
- Application Information
AI Technical Summary
Problems solved by technology
Method used
Image
Examples
Embodiment 1
[0033] like figure 2 and image 3 As shown, an improved structure of a push-in nut for a plug-in electrical connector, including a plastic body 11 of a plug-in electrical connector socket 1, and a plastic body 11 is formed on the surface where the plastic body and the plug 2 of the plug-in electrical connector are docked. The slot hole 12 having at least two straight planes A121 also includes a press-in nut 13 correspondingly pressed into the slot hole, and the press-in nut has a straight plane B131 corresponding to the straight plane A of the slot hole, Protrusions 132 are formed on the straight plane B of the press-in nut, undercuts 122 corresponding to the protrusions are formed on the straight plane A of the slot hole, and the press-in nut is pressed into the slot with interference Among them, the straight plane A fits with the straight plane B, and the convex point buckles with the undercut. In this way, by changing the traditional circular nut structure into a polygon...
Embodiment 2
[0038] see Figure 5 and Image 6 The difference between this embodiment 2 and embodiment 1 is that a soldering pin 133 is connected to the bottom of the press-in nut, and a via hole 124 corresponding to the soldering pin is formed at the bottom of the slot, and the soldering pin tightly fits through the vias. Preferably, the press-in nut is integrally formed with the welding pin. In this way, the welding pins can be welded together on the PCB when the product (plug-in electrical connector socket) is welded, so that the press-in nut is integrated with the PCB, thereby increasing the torque and pulling force.
[0039] The application of the plug-in electrical connector with the improved structure of the press-in nut in Embodiment 1 can be found in Figure 7 shown.
PUM
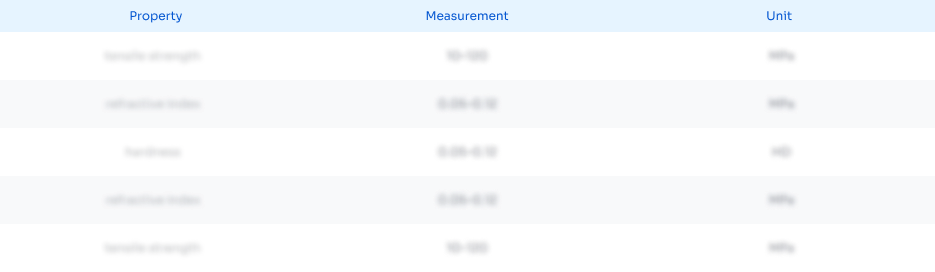
Abstract
Description
Claims
Application Information

- R&D
- Intellectual Property
- Life Sciences
- Materials
- Tech Scout
- Unparalleled Data Quality
- Higher Quality Content
- 60% Fewer Hallucinations
Browse by: Latest US Patents, China's latest patents, Technical Efficacy Thesaurus, Application Domain, Technology Topic, Popular Technical Reports.
© 2025 PatSnap. All rights reserved.Legal|Privacy policy|Modern Slavery Act Transparency Statement|Sitemap|About US| Contact US: help@patsnap.com