Hub electric driving system with torsion vibration attenuation function
An electric drive system, torsional vibration reduction technology, applied in the direction of electric components, electrical components, electromechanical devices, etc., can solve the problems affecting the ride comfort and ride comfort of the vehicle, the dynamic performance of the vehicle in all directions, and the torsional vibration of the transmission system, etc. problem, to achieve the effect of improving dynamic characteristics, avoiding resonance, and easy to arrange
- Summary
- Abstract
- Description
- Claims
- Application Information
AI Technical Summary
Problems solved by technology
Method used
Image
Examples
Embodiment 1
[0020] Such as figure 1 The hub motor drive system with torsional vibration damping function using outer rotor inner stator hub motor shown mainly includes hub motor 1, torsional vibration damping device 2, hub 8, rim 10, tire 11, brake 16, etc. Hub motor 1 includes: rotor support frame 1-1, rotor yoke 1-2, permanent magnet 1-3, stator core and winding 1-4, stator support frame 1-5; hub motor stator core and winding 1- 4 is supported on the support shaft 4 by the stator support frame, the permanent magnet 1-3 is glued to the surface of the rotor yoke 1-2, and the rotor yoke 1-2 is connected to the rotor support frame 1-2. The rotor support frame 1-2, the driven disc hub 2-4 and the driven disc 2-1 are all provided with circumferentially distributed rectangular windows, and each window is equipped with a corresponding elastic element 2-2, so as to Realize the elastic connection between the rotor support frame 1-2 and the driven disk hub 2-4 in the circumferential direction; th...
Embodiment 2
[0023] Such as figure 2 The shown in-wheel motor drive system with torsional vibration damping. its with figure 1 The difference is that the structure of the hub motor is an inner rotor and outer stator structure, and its working principle is the same as that of the electric wheel system using an outer rotor and inner stator hub motor, so it will not be repeated here.
PUM
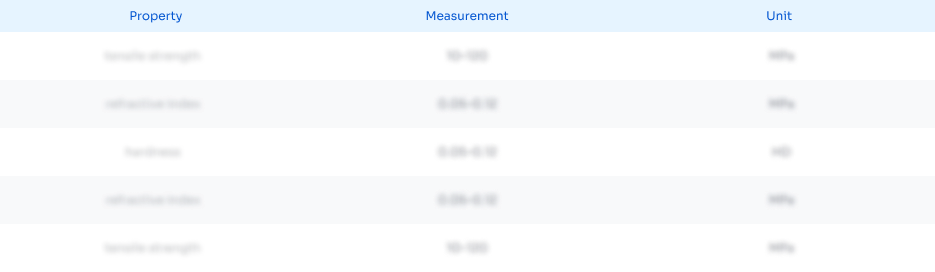
Abstract
Description
Claims
Application Information

- R&D
- Intellectual Property
- Life Sciences
- Materials
- Tech Scout
- Unparalleled Data Quality
- Higher Quality Content
- 60% Fewer Hallucinations
Browse by: Latest US Patents, China's latest patents, Technical Efficacy Thesaurus, Application Domain, Technology Topic, Popular Technical Reports.
© 2025 PatSnap. All rights reserved.Legal|Privacy policy|Modern Slavery Act Transparency Statement|Sitemap|About US| Contact US: help@patsnap.com