Capillary flow noise analysis and structural transformation design system
A technology for structural transformation and flow noise, applied in computer-aided design, design optimization/simulation, calculation, etc., can solve problems such as low efficiency, great impact on accuracy, and inability to comprehensively obtain capillary flow sound information.
- Summary
- Abstract
- Description
- Claims
- Application Information
AI Technical Summary
Problems solved by technology
Method used
Image
Examples
Embodiment Construction
[0043] The present invention will be further explained below in conjunction with specific embodiments.
[0044] refer to Figure 1-3 , the capillary flow noise analysis and structural transformation design system proposed by the present invention, comprising the following steps:
[0045] S1: Establish a parametric model of the capillary outlet, provide a parameter-driven capillary structure, and facilitate the realization of an automated process driven by an optimization algorithm;
[0046] S2: Start the optimization process, take the structural parameters as the design variables, and the capillary noise analysis results as the optimization target, and perform numerical analysis on the capillary structure corresponding to each structural parameter;
[0047] S3: Calculate the one-dimensional mathematical model of the capillary to obtain the one-dimensional flow state along the capillary, and on this basis, the inlet and outlet conditions of the outlet end of the capillary are gi...
PUM
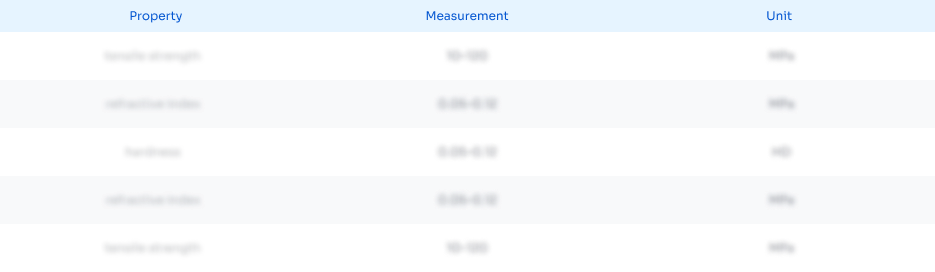
Abstract
Description
Claims
Application Information

- R&D Engineer
- R&D Manager
- IP Professional
- Industry Leading Data Capabilities
- Powerful AI technology
- Patent DNA Extraction
Browse by: Latest US Patents, China's latest patents, Technical Efficacy Thesaurus, Application Domain, Technology Topic, Popular Technical Reports.
© 2024 PatSnap. All rights reserved.Legal|Privacy policy|Modern Slavery Act Transparency Statement|Sitemap|About US| Contact US: help@patsnap.com