Method for identifying wave mechanical damage of high-speed milling cutter under intermittent impact load effect
A technology of damage identification and wave mechanics, applied in metal processing machinery parts, metal processing, measuring/indicating equipment, etc., can solve problems such as difficult to deduce macroscopic material physical characteristics, ignore control mechanism, and fail to deal with failure reasonably. Achieve the effect of solving multi-scale evolution problems
- Summary
- Abstract
- Description
- Claims
- Application Information
AI Technical Summary
Problems solved by technology
Method used
Image
Examples
Embodiment Construction
[0073] The specific embodiment of the present invention is described below in conjunction with each accompanying drawing:
[0074] refer to figure 1 , the high-speed milling cutter wave dynamics damage identification method under the intermittent impact load of the present invention is made of the following steps:
[0075] 1. Establish the transient cutting force model and particle dynamics equation of high-speed milling cutter
[0076] When the high-speed milling cutter is cutting, due to the intermittent cutting of the cutter teeth and the change of the cutting thickness, the cutting force whose waveform changes periodically becomes one of the main exciting forces that cause the vibration of the tool system. The milling process and transient cutting Force wave like figure 2 , image 3 as shown, figure 2 in, v f is the feed rate of the milling cutter, n is the speed of the milling cutter, k c,x 、k c,y 、k c,z are the modal stiffnesses along the three directions, resp...
PUM
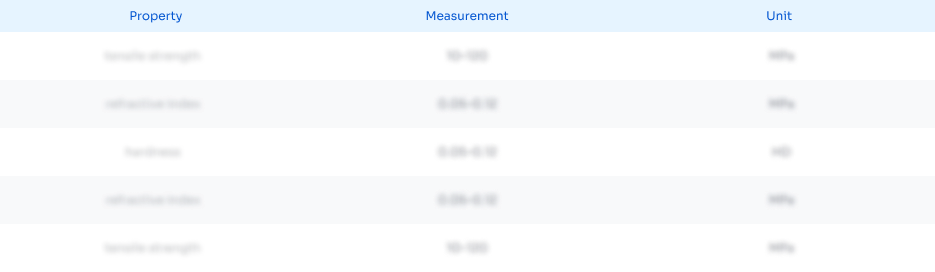
Abstract
Description
Claims
Application Information

- R&D Engineer
- R&D Manager
- IP Professional
- Industry Leading Data Capabilities
- Powerful AI technology
- Patent DNA Extraction
Browse by: Latest US Patents, China's latest patents, Technical Efficacy Thesaurus, Application Domain, Technology Topic, Popular Technical Reports.
© 2024 PatSnap. All rights reserved.Legal|Privacy policy|Modern Slavery Act Transparency Statement|Sitemap|About US| Contact US: help@patsnap.com