3D free bending forming technology optimization method for complex metal components
A bending forming and process optimization technology, which is applied in the field of 3D free bending forming process optimization of metal complex components, achieves obvious economic benefits, high production efficiency, and simple and feasible methods
- Summary
- Abstract
- Description
- Claims
- Application Information
AI Technical Summary
Problems solved by technology
Method used
Image
Examples
Embodiment 1
[0041] The first step is to divide the "L"-shaped elbow model with an outer diameter of 20mm, straight sections at both ends of 200mm, and a radius of 87.85mm into two straight sections and a curved (arc) section, such as image 3 As shown, they are respectively: the first straight section 1, the first curved section 3, and the second straight section 5;
[0042] In the second step, the first transition section 2 and the second transition section 4 are supplemented between the two straight sections and the curved sections;
[0043] In the third step, the axial feeding speed of the pipe is v=10mm / s, and the distance between the center of the bending die and the front end of the guiding mechanism is A=30mm. Establish the quantitative relationship between the geometric parameters of the first straight section, the first transition section, the first curved section, and the second transition section, such as bending radius R, bending angle θ, etc., and the moving speed u and movin...
Embodiment 2
[0059] The first step is to divide the "U"-shaped elbow with an outer diameter of 15mm, straight sections at both ends and the bottom of 200mm, and a radius of 63.75mm into three straight sections and two curved sections; Figure 4 As shown, they are: the third straight section 6, the fourth straight section 10, the fifth straight section 14, the second curved section 8, and the third curved section 12;
[0060] The second step, such as Figure 4 As shown, the transition section is supplemented between the straight section and the curved section. Since the "U"-shaped elbow is a left-right symmetrical structure, there are four transition sections in the elbow: the third transition section 7, the fourth transition section Section 9, the fifth transition section 11, the sixth transition section 13, and the process parameters of the third transition section 7 and the fifth transition section 11, the fourth transition section 9 and the sixth transition section 13 are completely con...
Embodiment 3
[0085] The first step is to divide the "S"-shaped elbow with an outer diameter of 15mm and two semicircle radii of 100mm into two curved sections, such as Figure 5 As shown, they are respectively the fourth curved section 16 and the fifth curved section 19;
[0086] The second step is to add 4 transition sections on the two semicircles, which are respectively: the seventh transition section 15, the eighth transition section 17, the ninth transition section 18, and the tenth transition section 20; wherein the seventh transition section 15 and the The process parameters of the ninth transition section 18, the eighth transition section 17 and the tenth transition section 20 are completely consistent;
[0087] In the third step, the axial feeding speed of the pipe is v=10mm / s, and the distance between the center of the bending die and the guide mechanism is A=22.5mm. Establish the quantitative relationship between the geometric shape parameters of the transition section and the ...
PUM
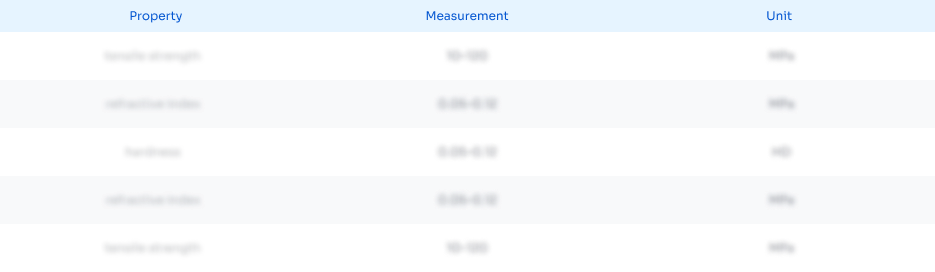
Abstract
Description
Claims
Application Information

- R&D
- Intellectual Property
- Life Sciences
- Materials
- Tech Scout
- Unparalleled Data Quality
- Higher Quality Content
- 60% Fewer Hallucinations
Browse by: Latest US Patents, China's latest patents, Technical Efficacy Thesaurus, Application Domain, Technology Topic, Popular Technical Reports.
© 2025 PatSnap. All rights reserved.Legal|Privacy policy|Modern Slavery Act Transparency Statement|Sitemap|About US| Contact US: help@patsnap.com