Mould head gasket for extrusion coater, extrusion mould head and extrusion coater
A coating machine and gasket technology, which is applied to the surface coating liquid device, coating, etc., can solve the problems of low production efficiency of pole pieces, improve accuracy and coating effect, improve utilization rate, reduce The effect of vacant areas
- Summary
- Abstract
- Description
- Claims
- Application Information
AI Technical Summary
Problems solved by technology
Method used
Image
Examples
Embodiment
[0028] Embodiment 1 of die head gasket for extrusion coating machine of the present invention, structural representation is as figure 1 , image 3 As shown, it includes a tail gasket 1 extending in the left-right direction and a left side gasket 20 and a right side gasket 21 respectively connected to both ends of the tail gasket 1. The left and right side gaskets include The vertical side and the horizontal side 4 that is arranged on the front end of the vertical side and turns inward in the opposite direction; two strip-shaped shunt gaskets 3 extending along the front and rear directions are arranged between the left and right side gaskets, and the strip-shaped shunt gasket 3 The rear end of the tail gasket is arranged on the tail gasket, and the front end has a chamfer; between the opposite sides of adjacent strip-shaped shunt gaskets, between the corresponding side of the shunt gasket at the edge position and the corresponding side of the corresponding side gasket Gasket s...
PUM
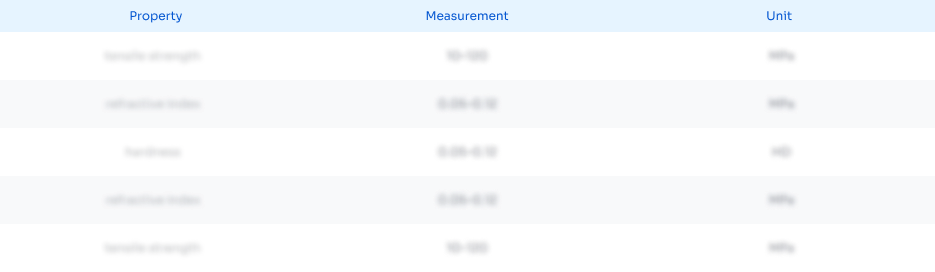
Abstract
Description
Claims
Application Information

- Generate Ideas
- Intellectual Property
- Life Sciences
- Materials
- Tech Scout
- Unparalleled Data Quality
- Higher Quality Content
- 60% Fewer Hallucinations
Browse by: Latest US Patents, China's latest patents, Technical Efficacy Thesaurus, Application Domain, Technology Topic, Popular Technical Reports.
© 2025 PatSnap. All rights reserved.Legal|Privacy policy|Modern Slavery Act Transparency Statement|Sitemap|About US| Contact US: help@patsnap.com