A kind of thickness layer paving structure and adjustment method of the direct bonding area of the trailing edge of the fan blade
A technology for adjusting the bonding area and thickness, which is applied to the thickness adjustment of the direct bonding area of the trailing edge of the wind turbine blade, and the thickness layer structure of the direct bonding area of the trailing edge of the wind turbine blade. The thickness is out of tolerance, the strength and service life are improved, and the effect is remarkable
- Summary
- Abstract
- Description
- Claims
- Application Information
AI Technical Summary
Problems solved by technology
Method used
Image
Examples
Embodiment 1
[0016] Embodiment 1, with reference to figure 1 , a layer structure for adjusting the thickness of the direct bonding area of the trailing edge of the fan blade: in the area where the direct bonding thickness of the trailing edge of the blade is out of tolerance, several layers of glass fiber cloth 2 are pre-embedded on the PS surface and the SS surface of this area, The glass fiber cloth is laid on the lower surface of the inner skin layer 3 and the upper surface of the unidirectional cloth layer 1 on both the PS surface and the SS surface, and the gentle transition of the edges is maintained when laying, forming several layers of pre-embedded glass fiber cloth. Adjusting the structural layer 4, the adjusting structural layer 4 is integrally formed with the casing layer by means of vacuum infusion.
[0017] The glass fiber cloth laid on the adjustment structure layer 4 is a biaxial glass fiber cloth or a triaxial glass fiber cloth, and the laying direction is from the blade...
Embodiment 2
[0018] Embodiment 2, a method for adjusting the thickness of the direct bonding area of the trailing edge of the fan blade, the steps are as follows:
[0019] (1) During the layering process of the shell, in the area where the direct bonding thickness of the trailing edge of the blade is out of tolerance, several layers of glass fiber cloth are pre-embedded on the PS and SS surfaces, and the glass fiber cloth is biaxial glass fiber cloth or triaxial To the glass fiber cloth, the laying direction is from the root of the blade to the tip of the blade;
[0020] (2) When the glass fiber cloth is laid, the starting point remains unchanged, and the end point is staggered layer by layer. The glass fiber cloth on the PS surface needs to be laid chordwise to fill the rear edge groove, and it is laid close to the rear edge parting line projection, and the glass fiber cloth on the SS surface is laid chordwise. The distance from the trailing edge parting line is 3-8mm. The glass fiber c...
PUM
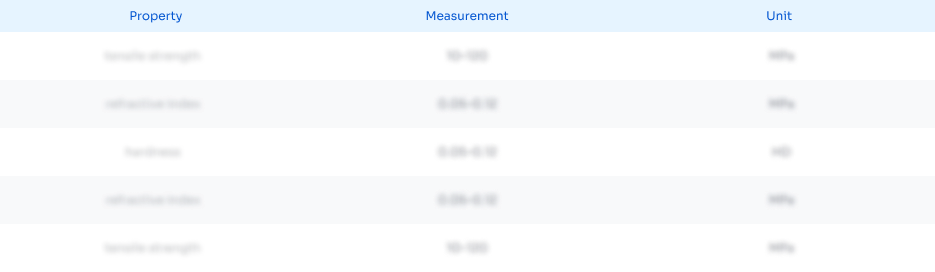
Abstract
Description
Claims
Application Information

- Generate Ideas
- Intellectual Property
- Life Sciences
- Materials
- Tech Scout
- Unparalleled Data Quality
- Higher Quality Content
- 60% Fewer Hallucinations
Browse by: Latest US Patents, China's latest patents, Technical Efficacy Thesaurus, Application Domain, Technology Topic, Popular Technical Reports.
© 2025 PatSnap. All rights reserved.Legal|Privacy policy|Modern Slavery Act Transparency Statement|Sitemap|About US| Contact US: help@patsnap.com