Machine vision assisted laser three-dimensional scanning and marking method
A laser three-dimensional and machine vision technology, applied in the direction of instruments, optical devices, measuring devices, etc., to achieve the effect of simple calibration steps, convenient marking and operation, and ensuring accuracy and reliability
- Summary
- Abstract
- Description
- Claims
- Application Information
AI Technical Summary
Problems solved by technology
Method used
Image
Examples
Embodiment Construction
[0018] In order to facilitate the understanding of those skilled in the art, the present invention will be further described below in conjunction with the embodiments and accompanying drawings, and the contents mentioned in the embodiments are not intended to limit the present invention.
[0019] The laser three-dimensional scanning marking method assisted by machine vision proposed by the present invention only needs the digital model of the marked three-dimensional curved surface w M and k (k≥n) visual feature points whose spatial position is known and whose relative position relationship with the three-dimensional surface is known.
[0020] refer to figure 1 As shown, the laser three-dimensional scanning marking method assisted by machine vision of the present invention is based on a marking system, which includes: an industrial camera whose imaging parameters have been calibrated, a laser scanning vibrating mirror and a computer; the laser scanning vibrating mirror include...
PUM
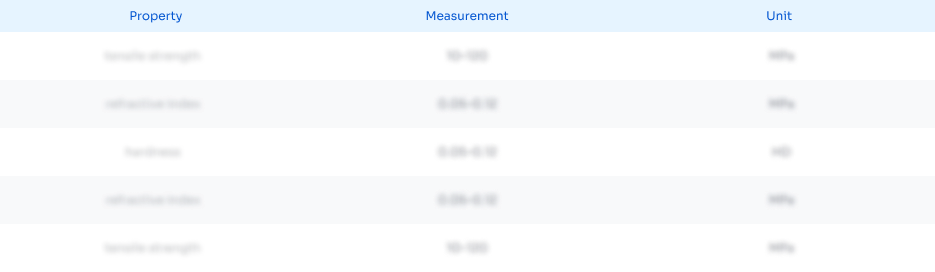
Abstract
Description
Claims
Application Information

- R&D Engineer
- R&D Manager
- IP Professional
- Industry Leading Data Capabilities
- Powerful AI technology
- Patent DNA Extraction
Browse by: Latest US Patents, China's latest patents, Technical Efficacy Thesaurus, Application Domain, Technology Topic, Popular Technical Reports.
© 2024 PatSnap. All rights reserved.Legal|Privacy policy|Modern Slavery Act Transparency Statement|Sitemap|About US| Contact US: help@patsnap.com