A method for controlling pressure in a refining furnace
A control method and internal pressure technology, applied in the direction of self-adaptive control, general control system, control/regulation system, etc., can solve the problems of increased production cost, unguaranteed anode plate quality, increased energy consumption, etc., and achieve energy saving consumption, demand reduction, and pressure maintenance
- Summary
- Abstract
- Description
- Claims
- Application Information
AI Technical Summary
Problems solved by technology
Method used
Image
Examples
Embodiment Construction
[0019] The present invention will be further described below in conjunction with the accompanying drawings and specific embodiments.
[0020] see figure 1 As shown, the refining furnace of the present invention includes a combustion furnace 1 and several reverberatory furnaces 2 arranged on the side of the combustion furnace 1. The combustion furnace 1 is connected with a main channel 3, and the main channel 3 is connected to each reverberatory furnace 2. An auxiliary channel 4 is arranged between the upper parts, and the main channel 3 is connected with a draft assembly, and the valve assembly 5 matched in the auxiliary channel 4 is arranged in the described auxiliary channel 4, and the combustion furnace 1 and the reverberatory furnace There are a number of pressure detection components inside the 2, and the valve component 5 is connected with the exhaust component, and there is a control component that controls the operation of the valve component 5 and the ventilation comp...
PUM
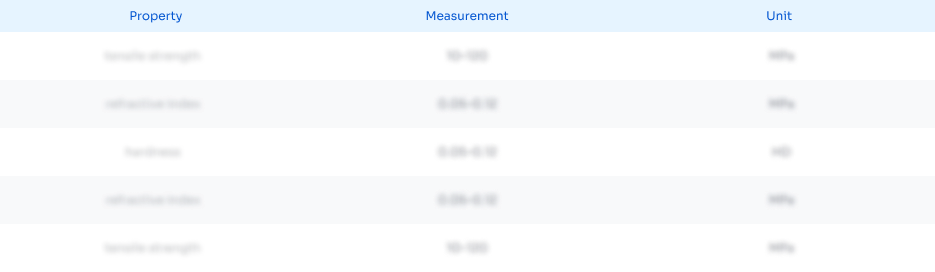
Abstract
Description
Claims
Application Information

- R&D
- Intellectual Property
- Life Sciences
- Materials
- Tech Scout
- Unparalleled Data Quality
- Higher Quality Content
- 60% Fewer Hallucinations
Browse by: Latest US Patents, China's latest patents, Technical Efficacy Thesaurus, Application Domain, Technology Topic, Popular Technical Reports.
© 2025 PatSnap. All rights reserved.Legal|Privacy policy|Modern Slavery Act Transparency Statement|Sitemap|About US| Contact US: help@patsnap.com