Socket and spigot type plastic pipe fusion welding device for conveying media through pressure
A medium-transporting, socket-type technology, applied in the direction of tubular objects, other household appliances, household appliances, etc., can solve the problems of difficult connection, waste of engineering materials and manpower, and prolonged construction period, so as to overcome the uneven connection strength and improve engineering. Progress, the effect of reducing labor intensity
- Summary
- Abstract
- Description
- Claims
- Application Information
AI Technical Summary
Problems solved by technology
Method used
Image
Examples
Embodiment Construction
[0010] Below in conjunction with accompanying drawing, the present invention will be further described:
[0011] See attached figure 1 , the whole device is arranged in the order of extruder 1, hot-melt material storage barrel 2, feed pipe 13, mold frame 5, and support 9, and mold frame 5 is provided with upper mold 6, lower mold 10, upper mold 6, One side of the lower mold 10 is provided with a sealing plate 12, the inner side of the sealing plate 12 is fixed with a mold core 12-1, and the mold core moving cylinder 3 fixed on one side of the mold frame 5 is connected with the sealing plate 12 and fixed on the mold frame 5 The upper mold moving cylinder 4 on the top is connected with the upper mold 6, and the lower mold moving cylinder 11 fixed under the mold base 5 is connected with the lower mold 10; there are two feeding lines between the sealing plate 12 and the mold core 12-1. Groove communicates with lower mold 10, the mold cavity formed when upper mold 6 and mold core ...
PUM
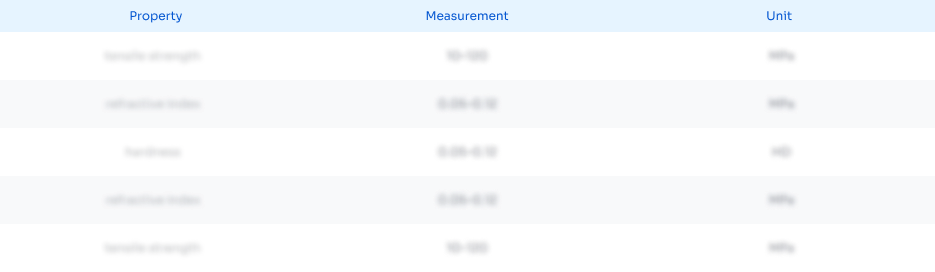
Abstract
Description
Claims
Application Information

- R&D
- Intellectual Property
- Life Sciences
- Materials
- Tech Scout
- Unparalleled Data Quality
- Higher Quality Content
- 60% Fewer Hallucinations
Browse by: Latest US Patents, China's latest patents, Technical Efficacy Thesaurus, Application Domain, Technology Topic, Popular Technical Reports.
© 2025 PatSnap. All rights reserved.Legal|Privacy policy|Modern Slavery Act Transparency Statement|Sitemap|About US| Contact US: help@patsnap.com