Flat belt type composite process and equipment
A compound process and flat belt technology, applied in the field of material compounding, can solve the problems affecting compound quality, bulky machine, different fastness, etc., to prolong the service life of the equipment, optimize the equipment, and ensure the effect of heating
- Summary
- Abstract
- Description
- Claims
- Application Information
AI Technical Summary
Problems solved by technology
Method used
Image
Examples
Embodiment Construction
[0035] Below in conjunction with example the present invention will be further described.
[0036] As shown in the figure, a kind of equipment used for flat belt composite process of the present invention includes: upper Teflon flat belt 1, upper heating plate 2, heating zone gap adjustment elevator 3, guide shaft 4, upper pressure roller 5, upper Cooling plate 6, flat belt upper frame 7, conveyor belt guide roller 8, upper belt driving roller 9, lower belt driving roller 10, upper driving roller servo motor 11, lower driving roller servo motor 12, lower cooling plate 13, lower pressure roller 14. Pressure roller gap adjustment motor 15, flat belt lower frame body 16, lower heating plate 17, upper belt passive roller 18, lower Teflon flat belt 19, bracket 20, slider 20-1, adjusting screw rod 20-1, lower Belt passive roller 21, composite material 22, heating zone gap adjustment motor 23, cooling zone gap adjustment motor 24, leaf spring 25, extension spring 26, cooling zone gap...
PUM
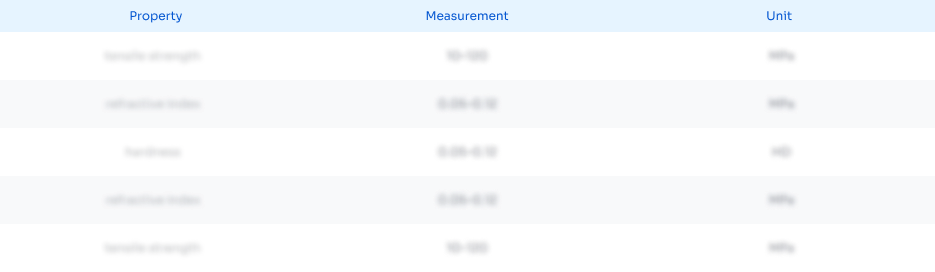
Abstract
Description
Claims
Application Information

- R&D
- Intellectual Property
- Life Sciences
- Materials
- Tech Scout
- Unparalleled Data Quality
- Higher Quality Content
- 60% Fewer Hallucinations
Browse by: Latest US Patents, China's latest patents, Technical Efficacy Thesaurus, Application Domain, Technology Topic, Popular Technical Reports.
© 2025 PatSnap. All rights reserved.Legal|Privacy policy|Modern Slavery Act Transparency Statement|Sitemap|About US| Contact US: help@patsnap.com