Dyeing preprocessing process of tatting chinlon cloth
A technology for dyeing pretreatment and brocade, which is applied in the field of dyeing pretreatment technology to achieve the effects of reducing energy consumption, reducing water consumption and improving the yield of finished products
- Summary
- Abstract
- Description
- Claims
- Application Information
AI Technical Summary
Problems solved by technology
Method used
Examples
Embodiment 1
[0013] A pre-dyeing process for woven nylon cloth, comprising the following steps: cold stacking→washing→ordering.
[0014] Among them, in the cold stacking process, the speed of the rolling car for rolling the liquid is 50m / min, the temperature of the immersion liquid in the rolling car is 40°C, and the immersion liquid contains sodium hydroxide, hydrogen peroxide, degreasing agent, degreasing yarn agent, Dispersant, hydrogen peroxide stabilizer, the amount of sodium hydroxide is 50g / L, the amount of hydrogen peroxide is 100g / L, the amount of degreasing agent is 10g / L, the amount of degreasing yarn agent is 7g / L, the amount of dispersant It is 7g / L, and the consumption of hydrogen peroxide stabilizer is 7g / L.
[0015] In the water washing step, the temperature is 50°C, 70°C, 85°C, 85°C, 90°C, 90°C, 75°C, 50°C, and 20°C in sequence.
[0016] In the process of cold stacking, the woven nylon cloth after padding is rolled up to form a cloth roll, and then the cloth roll is stack...
Embodiment 2
[0018] A pre-dyeing process for woven nylon cloth, comprising the following steps: cold stacking→washing→ordering.
[0019] Among them, in the cold stacking process, the speed of the rolling car for rolling the liquid is 40m / min, the temperature of the immersion liquid in the rolling car is 35°C, and the immersion liquid contains sodium hydroxide, hydrogen peroxide, degreasing agent, degreasing yarn agent, Dispersant, hydrogen peroxide stabilizer, the consumption of sodium hydroxide is 40g / L, the consumption of hydrogen peroxide is 90g / L, the consumption of degreaser is 8g / L, the consumption of degreasing yarn agent is 5g / L, the consumption of dispersant It is 5g / L, and the consumption of hydrogen peroxide stabilizer is 5g / L.
[0020] In the water washing step, the temperature is 50°C, 70°C, 85°C, 85°C, 90°C, 90°C, 75°C, 50°C, and 20°C in sequence.
[0021] In the process of cold stacking, the woven nylon cloth after padding is rolled up to form a cloth roll, and then the clo...
Embodiment 3
[0023] A pre-dyeing process for woven nylon cloth, comprising the following steps: cold stacking→washing→ordering.
[0024] Among them, in the cold stacking process, the speed of the rolling car for rolling the liquid is 60m / min, the temperature of the immersion liquid in the rolling car is 45°C, and the immersion liquid contains sodium hydroxide, hydrogen peroxide, degreasing agent, degreasing yarn agent, Dispersant, hydrogen peroxide stabilizer, the amount of sodium hydroxide is 60g / L, the amount of hydrogen peroxide is 110g / L, the amount of degreaser is 12g / L, the amount of degreasing yarn agent is 10g / L, the amount of dispersant It is 10g / L, and the consumption of hydrogen peroxide stabilizer is 10g / L.
[0025] In the water washing step, the temperature is 50°C, 70°C, 85°C, 85°C, 90°C, 90°C, 75°C, 50°C, and 20°C in sequence.
[0026] In the process of cold stacking, the woven nylon cloth after padding is rolled up to form a cloth roll, and then the cloth roll is stacked f...
PUM
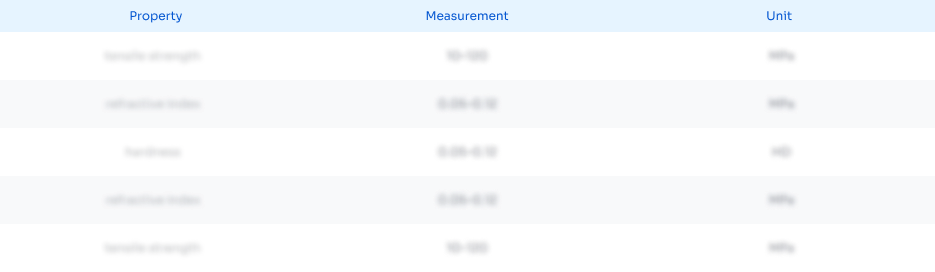
Abstract
Description
Claims
Application Information

- R&D
- Intellectual Property
- Life Sciences
- Materials
- Tech Scout
- Unparalleled Data Quality
- Higher Quality Content
- 60% Fewer Hallucinations
Browse by: Latest US Patents, China's latest patents, Technical Efficacy Thesaurus, Application Domain, Technology Topic, Popular Technical Reports.
© 2025 PatSnap. All rights reserved.Legal|Privacy policy|Modern Slavery Act Transparency Statement|Sitemap|About US| Contact US: help@patsnap.com