Vacuum-thrust-vector measurement system capable of adjusting rocket-motor swinging direction in real time
A rocket engine and thrust vectoring technology, which is used in engine testing, rocket engine installation, jet engine testing, etc., can solve problems such as engine geometric asymmetry, engine thrust action line deviating from the engine center axis, thrust eccentricity, etc., to eliminate The effect of friction resistance, reducing inter-directional interference, and facilitating decoupling
- Summary
- Abstract
- Description
- Claims
- Application Information
AI Technical Summary
Problems solved by technology
Method used
Image
Examples
Embodiment Construction
[0061] The present invention will be further described in detail below in conjunction with the accompanying drawings.
[0062] The lead screw A (251A) converts the rotational motion of the servo motor A (23A) into the linear motion of the ejector rod A (252A), resulting in the one-way force measurement and the length change of the motion control component A; the lead screw B (251B) converts the servo The rotary motion of the motor B (23B) is converted into the linear motion of the ejector rod B (252B), resulting in the one-way force measurement and the length change of the motion control component B; the screw C (251C) converts the rotary motion of the servo motor C (23C) Converted into the linear motion of the ejector rod C (252C), resulting in the length change of the one-way force measurement and motion control component C; the screw D (251D) converts the rotary motion of the servo motor D (23D) into the ejector rod D (252D) The linear motion of the unidirectional force mea...
PUM
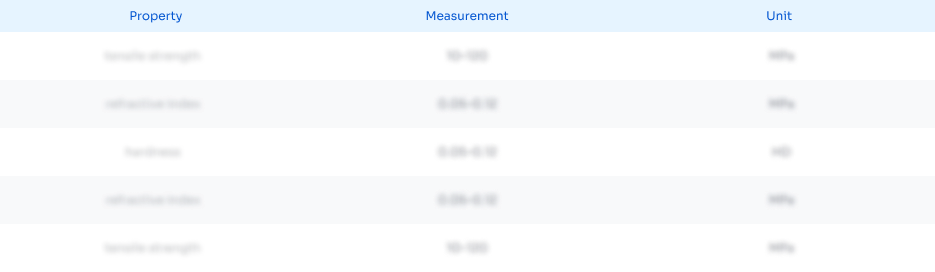
Abstract
Description
Claims
Application Information

- Generate Ideas
- Intellectual Property
- Life Sciences
- Materials
- Tech Scout
- Unparalleled Data Quality
- Higher Quality Content
- 60% Fewer Hallucinations
Browse by: Latest US Patents, China's latest patents, Technical Efficacy Thesaurus, Application Domain, Technology Topic, Popular Technical Reports.
© 2025 PatSnap. All rights reserved.Legal|Privacy policy|Modern Slavery Act Transparency Statement|Sitemap|About US| Contact US: help@patsnap.com