Threaded assembly structure for 3D printing plastic part
A threaded assembly and 3D printing technology, applied in the direction of threaded fasteners, nuts, connecting components, etc., can solve the problems of loose screws, self-tapping screws cannot be disassembled frequently, and screw columns burst, saving costs and simple screw locking. Reliable, energy-saving effect
- Summary
- Abstract
- Description
- Claims
- Application Information
AI Technical Summary
Problems solved by technology
Method used
Image
Examples
Embodiment Construction
[0016] The specific implementation of the present invention will be further described below in conjunction with the accompanying drawings and examples. The following examples are only used to illustrate the technical solutions of the present invention more clearly, but not to limit the protection scope of the present invention.
[0017] Such as figure 2 , image 3 , Figure 4 As shown, the technical solution of the present invention is to design a threaded assembly structure for 3D printed plastic parts, including plastic parts (12) with embedded metal nuts and round head screws (13).
[0018] Wherein the plastic parts (12) with pre-embedded metal nuts can be mass-produced through injection molding of plastic molds, and the thread type is made into standard parts; the round head screws (13) are ordinary machine screws.
[0019] The connection relationship is: the plastic part (12) of the embedded metal nut is inserted into the installation groove of the lower casing (14) fr...
PUM
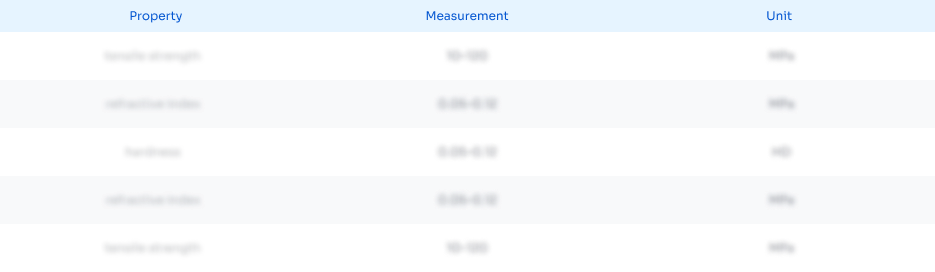
Abstract
Description
Claims
Application Information

- R&D Engineer
- R&D Manager
- IP Professional
- Industry Leading Data Capabilities
- Powerful AI technology
- Patent DNA Extraction
Browse by: Latest US Patents, China's latest patents, Technical Efficacy Thesaurus, Application Domain, Technology Topic, Popular Technical Reports.
© 2024 PatSnap. All rights reserved.Legal|Privacy policy|Modern Slavery Act Transparency Statement|Sitemap|About US| Contact US: help@patsnap.com