Method for preparing acrylic acid catalyst by using propane
A catalyst, acrylic acid technology, applied in the preparation of organic compounds, the preparation of carboxylates, chemical instruments and methods, etc., can solve the problems of easy breakage, easy blockage, affecting the long-term use effect of catalysts, etc. active effect
- Summary
- Abstract
- Description
- Claims
- Application Information
AI Technical Summary
Problems solved by technology
Method used
Examples
Embodiment 1
[0014] 1) In the reactor, add 100 parts by weight of styrene, 60 parts of divinylbenzene, 3 parts of cyclopentadienyl titanium trichloride, 4 parts of bis(tricarbonyl cyclopentadiene molybdenum), 2 parts Part cyclopentadiene tricarbonyl rhenium, 0.3 part trimethylcyclopentadiene platinum, 0.3 part lithium pentamethylcyclopentadiene, 0.2 part bis(pentamethylcyclopentadiene) cobalt, 2000 parts water , 2 parts of polyvinyl alcohol, 1 part of benzoyl peroxide, reacted at 87 ° C for 8 hours, filtered, and dried to obtain an intermediate product;
[0015] 2) In parts by weight, add 4 parts of 1-5 dimethyl diselenide and 20 parts of toluene to 100 parts of the intermediate product, react at 10°C for 2 hours, filter, and dry to obtain the catalyst product. Numbered M-1.
Embodiment 2
[0017] 1) In the reactor, add 100 parts by weight of styrene, 50 parts of divinylbenzene, 1 part of cyclopentadienyl titanium trichloride, 1 part of bis(tricarbonyl cyclopentadiene molybdenum), 1 Part cyclopentadiene tricarbonyl rhenium, 0.1 part trimethylcyclopentadiene platinum, 0.1 part lithium pentamethylcyclopentadiene, 0.1 part bis(pentamethylcyclopentadiene) cobalt, 1000 parts water , 1 part of polyvinyl alcohol, 0.5 part of benzoyl peroxide, reacted at 80 ° C for 12 hours, filtered, and dried to obtain an intermediate product;
[0018] 2) In parts by weight, add 1 part of 1-5 dimethyl diselenide and 10 parts of toluene to 100 parts of the intermediate product, react at 0°C for 5 hours, filter, and dry to obtain the catalyst product. Numbered M-2.
Embodiment 3
[0020] 1) In the reactor, add 100 parts by weight of styrene, 80 parts of divinylbenzene, 10 parts of cyclopentadienyl titanium trichloride, 10 parts of bis(tricarbonyl cyclopentadiene molybdenum), 5 parts Part cyclopentadiene tricarbonyl rhenium, 0.5 part trimethylcyclopentadiene platinum, 0.5 part lithium pentamethylcyclopentadiene, 0.5 part bis(pentamethylcyclopentadiene) cobalt, 3000 parts water , 4 parts of polyvinyl alcohol, 2 parts of benzoyl peroxide, reacted at 95 ° C for 5 hours, filtered, and dried to obtain an intermediate product;
[0021] 2) In parts by weight, add 10 parts of 1-5 dimethyl diselenide and 30 parts of toluene to 100 parts of the intermediate product, react at 30° C. for 1 hour, filter, and dry to obtain the catalyst product. Numbered M-3.
PUM
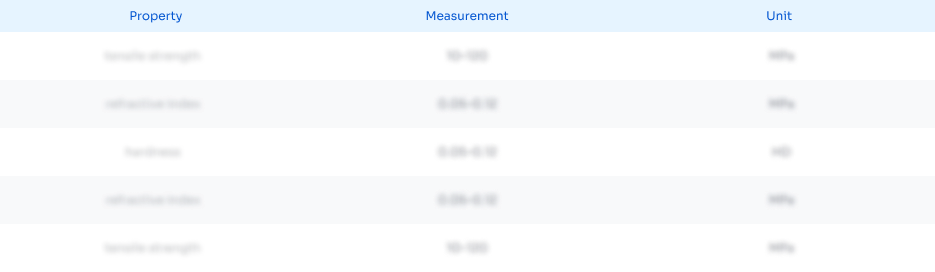
Abstract
Description
Claims
Application Information

- R&D Engineer
- R&D Manager
- IP Professional
- Industry Leading Data Capabilities
- Powerful AI technology
- Patent DNA Extraction
Browse by: Latest US Patents, China's latest patents, Technical Efficacy Thesaurus, Application Domain, Technology Topic, Popular Technical Reports.
© 2024 PatSnap. All rights reserved.Legal|Privacy policy|Modern Slavery Act Transparency Statement|Sitemap|About US| Contact US: help@patsnap.com