Diesel tail gas treating agent production method
A technology for tail gas treatment and production methods, which is applied in gas treatment, separation methods, chemical instruments and methods, etc., to achieve the effects of wide source of raw materials, remarkable treatment effect, and remarkable purification effect.
- Summary
- Abstract
- Description
- Claims
- Application Information
AI Technical Summary
Problems solved by technology
Method used
Examples
Embodiment 1
[0026] A production method of a diesel engine exhaust treatment agent, comprising the following steps:
[0027] (1) Ingredients: Weigh 30kg of urea, 80kg of high-purity water, 8kg of methanol, 4kg of oxalic acid amide and 2kg of cocamidopropyl betaine;
[0028] (2) Dissolution: Mix urea and high-purity water, and stir for 20 minutes at a temperature of 55°C and a rotation speed of 250r / min to obtain a urea solution;
[0029] (3) Adsorption and impurity removal: add 3 kg of cellulose xanthate adsorbent to the above urea solution, continue stirring for 40 minutes, and then filter to remove solid impurities to obtain a clarified urea solution;
[0030] (4) Membrane filtration: filter the clarified urea solution with a nanofiltration membrane with a pore size of 1 nm to obtain a pure urea solution;
[0031] (5) Mixing: Mix the pure urea solution with the above-mentioned methanol, oxalic acid amide and cocamidopropyl betaine at a speed of 250r / min for 30min to obtain the diesel en...
Embodiment 2
[0036] A production method of a diesel engine exhaust treatment agent, comprising the following steps:
[0037] (1) Ingredients: Weigh 35kg of urea, 90kg of high-purity water, 10kg of methanol, 5kg of oxalic acid amide and 3kg of cocamidopropyl betaine;
[0038] (2) Dissolution: Mix urea and high-purity water, and stir for 15 minutes at a temperature of 60°C and a rotation speed of 300r / min to obtain a urea solution;
[0039] (3) Adsorption and impurity removal: Add 4kg of cellulose xanthate adsorbent to the above urea solution, continue to stir for 30min, then filter to remove solid impurities to obtain a clarified urea solution;
[0040] (4) Membrane filtration: filter the clarified urea solution with a nanofiltration membrane with a pore size of 1 nm to obtain a pure urea solution;
[0041] (5) Mixing: Mix the pure urea solution with the above-mentioned methanol, oxalic acid amide and cocamidopropyl betaine at a rotation speed of 300r / min for 40min to obtain the diesel eng...
Embodiment 3
[0046] A production method of a diesel engine exhaust treatment agent, comprising the following steps:
[0047] (1) Ingredients: Weigh 40kg of urea, 100kg of high-purity water, 12kg of methanol, 3kg of oxalic acid amide and 5kg of cocamidopropyl betaine;
[0048] (2) Dissolution: Mix urea and high-purity water, and stir for 20 minutes at a temperature of 65°C and a rotation speed of 350r / min to obtain a urea solution;
[0049] (3) Adsorption and impurity removal: Add 5 kg of cellulose xanthate adsorbent to the above urea solution, continue to stir for 20 minutes, and then filter to remove solid impurities to obtain a clarified urea solution;
[0050] (4) Membrane filtration: filter the clarified urea solution with a nanofiltration membrane with a pore size of 2nm to obtain a pure urea solution;
[0051] (5) Mixing: Mix the pure urea solution with the above-mentioned methanol, oxalic acid amide and cocamidopropyl betaine at a speed of 350r / min for 20min to obtain the diesel en...
PUM
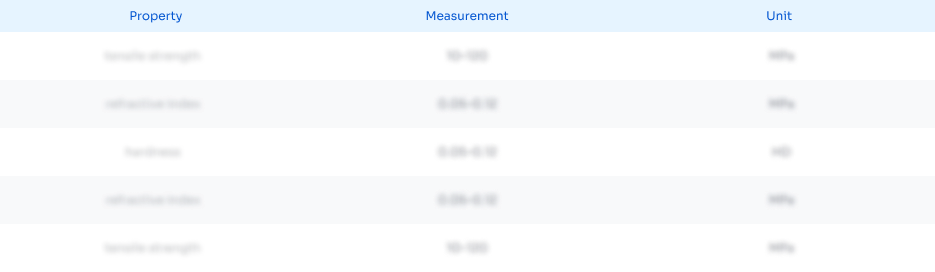
Abstract
Description
Claims
Application Information

- R&D
- Intellectual Property
- Life Sciences
- Materials
- Tech Scout
- Unparalleled Data Quality
- Higher Quality Content
- 60% Fewer Hallucinations
Browse by: Latest US Patents, China's latest patents, Technical Efficacy Thesaurus, Application Domain, Technology Topic, Popular Technical Reports.
© 2025 PatSnap. All rights reserved.Legal|Privacy policy|Modern Slavery Act Transparency Statement|Sitemap|About US| Contact US: help@patsnap.com