Catalyst for preparing vinyl chloride by cracking 1,2-dichloroethane as well as preparation method and application of catalyst
A dichloroethane and catalyst technology, applied in the direction of dehydrohalogenation preparation, etc., can solve the problems of low conversion rate and unstable performance, and achieve the effects of good catalytic performance, simple preparation process, and cheap and easy-to-obtain raw materials
- Summary
- Abstract
- Description
- Claims
- Application Information
AI Technical Summary
Problems solved by technology
Method used
Examples
Embodiment 1
[0032] Prepare sample 1
[0033] 1. Dissolve 20g of urea in 100ml of water to make a solution.
[0034] 2. Add 100g of activated carbon to the above solution and soak under normal pressure, so that the solution can fully penetrate into the interior of the activated carbon. The soaking temperature is 30° C., and the soaking time is 3 hours.
[0035] 3. Dry the soaked activated carbon and its load at 120°C to fully volatilize the solvent.
[0036] 4. Roast the dried activated carbon in a tube furnace at high temperature under the protection of nitrogen at a temperature of 550°C and a heating rate of 5°C / min, and cool to room temperature.
[0037] The sample 1 prepared by the above steps has a mass percentage of nitrogen-containing compounds of 16.7%.
Embodiment 2
[0039] Prepare sample 2
[0040] 1. Dissolve 40g of urea in 100ml of water to make a solution.
[0041] 2. Add 100g of activated carbon into the above solution for soaking, and soak under normal pressure so that the solution can fully penetrate into the activated carbon. The soaking temperature is 30° C., and the soaking time is 4 hours.
[0042] 3. Dry the soaked activated carbon and its load at 120°C to fully volatilize the solvent.
[0043] 4. Roast the dried activated carbon in a tube furnace at high temperature under the protection of nitrogen at a temperature of 550°C and a heating rate of 5°C / min, and cool to room temperature.
[0044] The mass percentage of nitrogen-containing compound in sample 2 prepared in the above steps is 28.6%.
Embodiment 3
[0046] Prepare sample 3
[0047] 1. Dissolve 50g of urea in 100ml of water to make a solution.
[0048] 2. Add 100g of activated carbon to the above solution and soak under normal pressure, so that the solution can fully penetrate into the interior of the activated carbon. The soaking temperature is 30° C., and the soaking time is 3 hours. .
[0049] 3. Dry the soaked activated carbon and its load at 120°C to fully volatilize the solvent.
[0050] 4. Roast the dried activated carbon in a tube furnace at high temperature under the protection of nitrogen at a temperature of 550°C and a heating rate of 5°C / min, and cool to room temperature.
[0051] The mass percentage of nitrogen-containing compound in sample 3 prepared by the above steps is 33.3%.
PUM
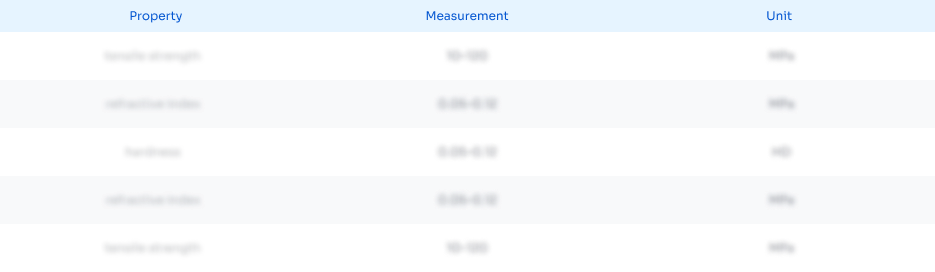
Abstract
Description
Claims
Application Information

- Generate Ideas
- Intellectual Property
- Life Sciences
- Materials
- Tech Scout
- Unparalleled Data Quality
- Higher Quality Content
- 60% Fewer Hallucinations
Browse by: Latest US Patents, China's latest patents, Technical Efficacy Thesaurus, Application Domain, Technology Topic, Popular Technical Reports.
© 2025 PatSnap. All rights reserved.Legal|Privacy policy|Modern Slavery Act Transparency Statement|Sitemap|About US| Contact US: help@patsnap.com