A smart energy large-scale composite core pultrusion process and device
A technology of smart energy and pultrusion technology, which is applied in the manufacture of electrical components, circuits, cables/conductors, etc., can solve the problems of slow pultrusion speed, excessive surface resin curing, and insufficient internal curing degree of large-scale composite cores, etc., to achieve guaranteed Resin amount stability, reduced contact, and improved quality stability
- Summary
- Abstract
- Description
- Claims
- Application Information
AI Technical Summary
Problems solved by technology
Method used
Image
Examples
Embodiment 1
[0025] See figure 1 , a smart energy large-scale composite core pultrusion device in this embodiment, including a yarn splitter 1, a main dipping tank 2, a extrusion roller 3, a yarn collector 4, a curing mold 5, a pre-curing mold 6, a first Secondary dipping tank 7, scraper 8, second secondary dipping tank 9 and pressure roller; main dipping tank 2 includes main dipping tank No. 1 slot 21 and main dipping tank No. 2 slot 22; pre-curing The mold 6 is arranged above the main dipping tank 2, and comprises a first pre-curing mold 61, a second pre-curing mold 62 and a third pre-curing mold 63 arranged in sequence; the scraper 8 includes a first scraper 81, a second The scraper 82 and the third scraper 83 are respectively arranged at the entrances of the three pre-curing molds. The yarn divider 1 includes a first yarn divider 11, a second yarn divider 12, a third yarn divider 13 and a fourth yarn divider 14, which are respectively arranged in the No. 2 slot 22 of the main dipping ...
PUM
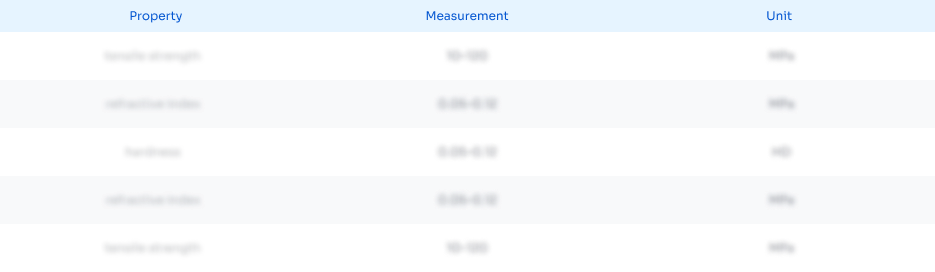
Abstract
Description
Claims
Application Information

- R&D
- Intellectual Property
- Life Sciences
- Materials
- Tech Scout
- Unparalleled Data Quality
- Higher Quality Content
- 60% Fewer Hallucinations
Browse by: Latest US Patents, China's latest patents, Technical Efficacy Thesaurus, Application Domain, Technology Topic, Popular Technical Reports.
© 2025 PatSnap. All rights reserved.Legal|Privacy policy|Modern Slavery Act Transparency Statement|Sitemap|About US| Contact US: help@patsnap.com