A kind of fly ash pre-selected iron concentrate to improve grade and reduce sio 2 content method
A technology for improving grade and iron concentrate, applied in chemical instruments and methods, wet separation, solid separation, etc., can solve the problems of low grade of iron concentrate, high production cost, restricted promotion and application, etc. High iron recovery rate and the effect of improving iron grade
- Summary
- Abstract
- Description
- Claims
- Application Information
AI Technical Summary
Problems solved by technology
Method used
Image
Examples
Embodiment 1
[0017] Take the boiler fly ash of the 42.5MW unit boiler of JISCO Hongsheng Thermal Power No. 2 Mass percentage composition 54.21%, carry out following treatment:
[0018] A: The fly ash produced by the thermal power plant is subjected to dry pre-selection treatment, the pre-selected magnetic field strength is 400mT, and the iron grade is 43.02%, SiO 2 Pre-selected iron ore concentrate with a mass percentage of 14.36%;
[0019] B: The above-mentioned pre-selected iron concentrate is divided into coarse and fine grades by a high-fineness grading cyclone. Only 19.14%, SiO 2 The mass percentage content is 27.45%, so it is excluded. The iron grade of the -400 mesh pre-selected iron concentrate is 50.12%, the iron distribution rate is 80.86%, and the SiO 2 The mass percentage is 11.56%, which is sent to the next link for weak magnetic selection;
[0020] C: The above -400 mesh fly ash pre-selected iron concentrate is subjected to weak magnetic concentration by two-stage magneti...
Embodiment 2
[0022] Take the boiler fly ash of the 2×300MW unit boiler of JISCO Hongsheng Thermal Power Plant No. 2 Mass percentage composition 46.23%, carry out following treatment:
[0023] A: The fly ash produced by the thermal power plant is subjected to dry pre-selection treatment, the pre-selected magnetic field strength is 400mT, and the iron grade is 44.21%, SiO 2 Pre-selected iron ore concentrate with a mass percentage of 13.86%;
[0024] B: The above-mentioned pre-selected iron concentrate is divided into coarse and fine grades by a high-fineness grading cyclone. Only 20.63%, SiO 2 The mass percentage content is 25.31%, so it is excluded. The iron grade of the -400 mesh pre-selected iron concentrate is 52.06%, the iron distribution rate is 79.37%, and the SiO 2 The mass percentage is 10.59%, which is sent to the next link for weak magnetic selection;
[0025] C: The above -300 mesh fly ash pre-selected iron concentrate is subjected to weak magnetic concentration by two-stage ...
Embodiment 3
[0027] Take the boiler fly ash of the 2×350MW unit boiler of JISCO Hongsheng Thermal Power Plant No. 2, the grade of the fly ash is 9.64% iron, SiO 2 Mass percentage composition 38.21%, carry out following treatment:
[0028] A: The fly ash produced by the thermal power plant is subjected to dry pre-selection treatment, the pre-selected magnetic field strength is 300 mT, and the iron grade is 46.32%, SiO 2 Pre-selected iron ore concentrate with a mass percentage of 13.07%;
[0029] B: The above-mentioned pre-selected iron concentrate is divided into coarse and fine grades by a high-fineness grading cyclone. The grade size is 300 mesh. Only 18.63%, SiO 2 The mass percentage content is 27.68%, so it is excluded. The iron grade of the -300 mesh size pre-selected iron concentrate is 53.44%, the iron distribution rate is 81.37%, and the SiO 2 The mass percentage is 10.48%, which is sent to the next link for weak magnetic selection;
[0030] C: The above -300 mesh fly ash pre-se...
PUM
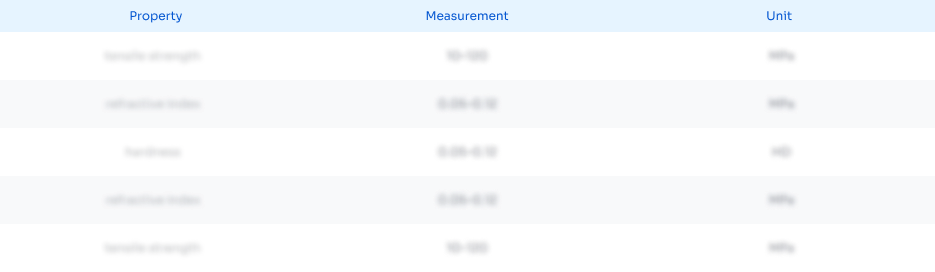
Abstract
Description
Claims
Application Information

- Generate Ideas
- Intellectual Property
- Life Sciences
- Materials
- Tech Scout
- Unparalleled Data Quality
- Higher Quality Content
- 60% Fewer Hallucinations
Browse by: Latest US Patents, China's latest patents, Technical Efficacy Thesaurus, Application Domain, Technology Topic, Popular Technical Reports.
© 2025 PatSnap. All rights reserved.Legal|Privacy policy|Modern Slavery Act Transparency Statement|Sitemap|About US| Contact US: help@patsnap.com